Award winning: Exemplary integration of vehicle orders and material supply
Opel has once again been recognized for its innovative drive. At the Third Forum Automotive Logistics in Leipzig, jury-chairman Professor Dr. Wolfgang Stölzle presented Michael Scholl, Director Supply Chain at Opel with the ‘2015 VDA Logistics Award. It is the eighth time that the German Association of the Automotive Industry (VDA) has presented the award to a company for its intelligent logistics system that can serve as a model for other players in the automotive industry.
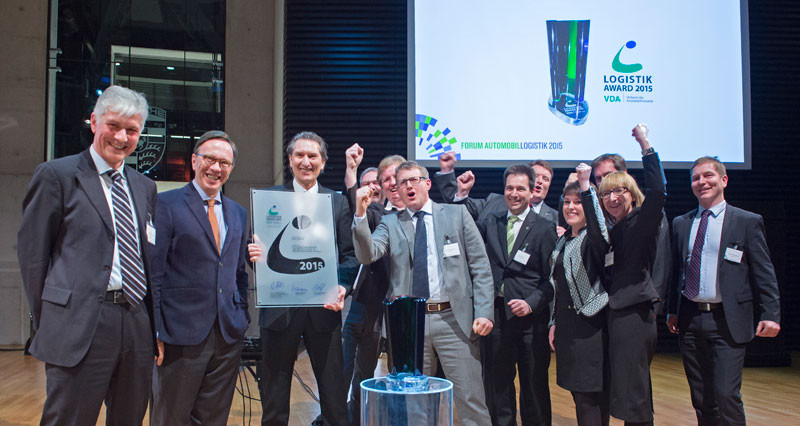
“The system assists us to meet customer requirements on schedule while staying flexible. It also allows us to optimize the value chain and the production program. We can react quickly and flexibly to changing conditions while maintaining complete transparency,” said Michael Scholl, Director Supply Chain at Opel, at the award ceremony in Leipzig.
Vehicle orders and material supply are the two central areas of work for logistics experts in the automotive industry. Opel succeeded in creating a close network between these two areas both organizationally and procedurally. The most important feature of the new system is that incoming vehicle orders for the production plants are controlled simultaneously in real-time under consideration of material availability, especially the material pipeline of overseas suppliers. Thus, order scheduling is no longer sequential but instead integrated. This also enables Opel to react quicker to changing conditions.
“This innovative solution is further proof for our `change your mind´ approach at Opel and our willingness to change the corporate culture. We changed organizational structures and, thanks to a cross-divisional team, introduced a system that allows outstanding flexibility – for the benefit of our customers,” said Katherine Worthen, Vice President, Purchasing and Supply Chain, Opel Group GmbH.
The new system offers countless advantages such as transparency, flexibility, low material stocks and reduction of special material shipment to name but a few. Elsewhere, the customer also benefits from it because vehicle delivery dates can be maintained with even higher accuracy.
The system was developed by a cross-divisional Opel team, consisting of experts from logistics, materials management, order management, and IT in cooperation with IT service provider Flexis AG from Stuttgart. It enables a future period preview of 40 weeks and considers roughly 45,000 part numbers for 20 Opel models made in seven European production plants.