FEV dynamic simulation software delivers extended functionality for gear set and journal bearing analyses
Aachen based engineering service provider FEV has launched a new release of the “FEV Virtual Engine” simulation software for advanced powertrain dynamics analysis. In addition to a number of improvements for cranktrain analysis, version 23 offers solutions for Elastohydrodynamic (EHD) bearings as well as expanded 3D dynamic gear analysis. “With the new release, we have added important functionality to FEV Virtual Engine that allows significant test cell development work to be replaced by simulation”, explained Professor Stefan Pischinger, President and CEO of FEV Group. “Virtual Engine optimizes powertrain development through reliable prediction of dynamics and, thereby, effectively reduces the development time.” For further information please contact Mustafa Duyar, Product Business Manager for FEV Virtual Engine (duyar@fev.com).
“FEV Virtual Engine” software has been available since 2008 and uses a template-based structure that combines the advantages of easy-to-use special-purpose software with the efficiency of universal dynamic simulation software offering additional extendability.
“The extensive modeling options of FEV Virtual Engine not only facilitate the analysis of every part of conventional powertrain systems, but also of new and innovative designs – for example, from belt-driven start / stop systems up to complete hybrid drives,” said Mustafa Duyar, Product Business Manager for FEV Virtual Engine.
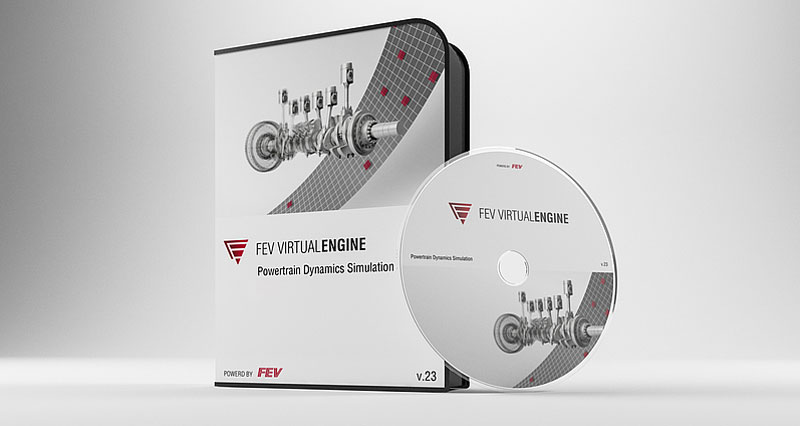
3D gear dynamic analysis in the concept and detailing phase
Virtual Engine 23 includes a new analytical approach for the 3-dimensional dynamic simulation of gears. This approach includes a detailed tooth contact analysis with simultaneous consideration of the overall system dynamics in 3D space. Thus, the user receives detailed values for durability and NVH behavior for the individual components. The results also include factors such as torsional stiffness and pressure, condition of the oil film – including the influence of lubricant type and temperature – as well as gear rattle and whine. This allows the modeling effort and simulation time to be optimized in both the conceptual and the specification phase.
Elastohydrodynamic plain bearing simulation
Plain bearings must withstand high dynamic oil pressures that cause local deformations and, thus, directly affect their ability to function properly. Using an extensive detailed dynamic analysis, taking into account the Elastohydrodynamic bearing performance can now be accurately simulated.
“In addition to these advanced analysis functions, the new release includes a first milestone for the kinematic analysis of the valvetrain and many enhancements to the cranktrain mechanism,” says Duyar.