The established model for mass production, where dedicated facilities deliver the maximum output with consistent quality at the lowest cost, worked fine for stable product lines and predictable future demand. It is woefully ill equipped for today’s turbulent marketplace. Three factors have combined to create a perfect storm: increasing model diversity, accelerating technology development and unpredictable consumer demand.
During the current decade, internal combustion engines (ICE) running on gasoline, diesel or alternative fuels, fuel cells, BEVs and hybrids will compete in the marketplace. The sales volume split, and hence the manufacturing output, for the different variants will depend on such factors as regional legislation on emissions and taxation, consumer appetite for the product and the pace of technical development. The supply chain also faces uncertainty, for example as the preferred battery technology changes.
Ensuring production facilities are future-proofed against fluctuations in product mix and volumes could well make the difference between corporate success or failure
The evolution of propulsion technology is now so rapid that today’s optimum powertrain may become uncompetitive within just a year or two; the manufacturing solutions chosen for that powertrain at the outset may have to be re-visited as the vehicles themselves are re-designed. Fundamental decisions, such as ‘kitting’ assemblies at suppliers or completing them in-house may be reversed. This level of change is unthinkable with traditional dedicated facilities.
Commercial survival in future will require flexibility and agility; the capacity to switch production volumes and product mix rapidly, while remaining cost-competitive. This requires a change in mindset from the customary approach to facility planning. The most effective way to accommodate uncertainty is to switch from conventional ‘long line’ production to manufacturing cells which can be quickly brought on stream or reprogrammed and repurposed, to adapt to fluctuations in demand.
The traditional line may still be appropriate for final assembly, but should be supported by flexible cells that do not require changes to the overall facility and, more importantly, can be repurposed without loss of manufacturing output. One way to ensure the cells are successfully changed is to introduce as much automation as possible. AGRs (Automated Guided Robots) and AMRs (Autonomous Mobile Robots) will become critical in ensuring a smooth transition.
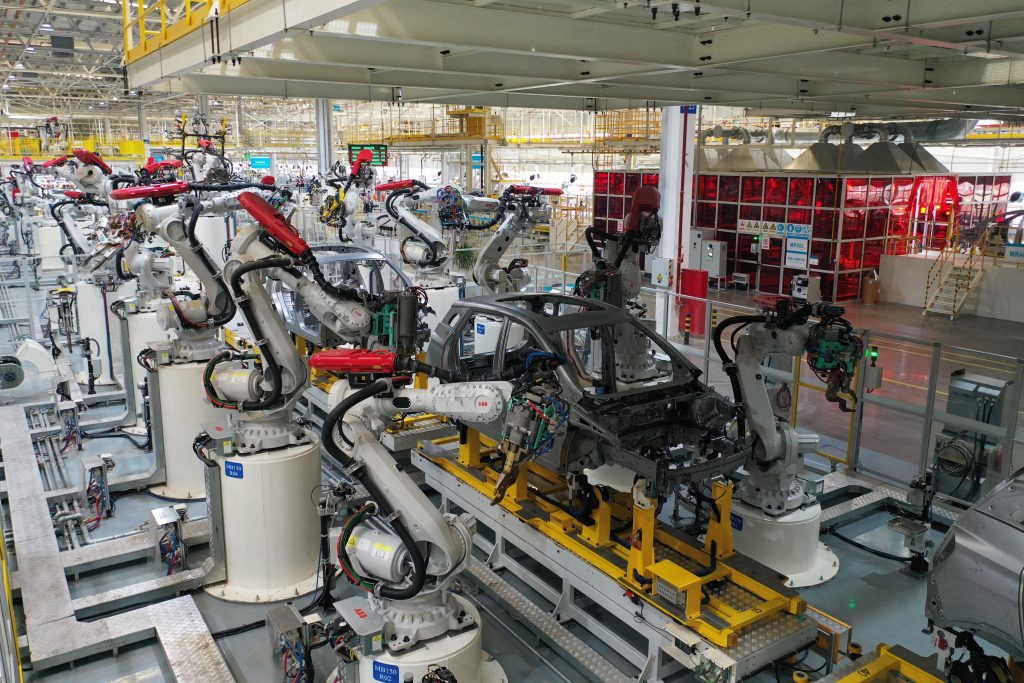
New facilities can be specified, evaluated and commissioned much more quickly than previously, thanks to developments in simulation. Every aspect of a manufacturing cell’s operation can be modelled virtually, then the effects of any changes studied to validate the consistency and quality of the output. This allows much quicker calibration of a new facility, with shorter commissioning time, and means new products can be brought on stream more quickly, eliminating unexpected issues almost completely.
By starting with a single cell to validate the approach and set production standards, all parameters can be optimised without disrupting existing manufacturing. Additional duplicate cells can be added as necessary to keep pace with the required rates of production as demand increases. This smooths out both ramp up and ramp down, and ensures flexibility is retained throughout a plant’s life, since cells can be decommissioned, moved or repurposed.
Such is the level of change in today’s automotive market, ensuring production facilities are future-proofed against fluctuations in product mix and volumes could well make the difference between corporate success or failure.
The opinions expressed here are those of the author and do not necessarily reflect the positions of Automotive World Ltd.
Joerg Reger is Managing Director of ABB Robotics’ automotive OEM business line
The Automotive World Comment column is open to automotive industry decision makers and influencers. If you would like to contribute a Comment article, please contact editorial@automotiveworld.com