Since its introduction in the 1990s, the use of hot stamping has been steadily gaining popularity across the automotive industry. As the technology develops, and its benefits increasingly justify the upfront investment costs, hot stamped parts are appearing not only on large premium cars, but also on small, mainstream and even low-cost cars.
Hot stamping is used to produce safety-critical structural parts, such as bumper beams, door and A- and B-pillar reinforcements, and roof and dash panel cross members. Its main attraction is that it offers the associated benefits of weight reduction and the production of higher strength parts. As a result, hot stamping is now widely regarded as a mainstream manufacturing technique.
“The question is how quickly OEMs not currently using many hot stamped parts will close the gap with the best in the industry,” says Jean-Luc Thirion, Head of Automotive Product Portfolio, Global Research and Development, ArcelorMittal.
“Hot stamping is a cost-effective technology enabling the production of high-strength complex parts without too many processing issues. Hot stamping technology, and Usibor, [ArcelorMittal’s proprietary 1500MPa steel grade developed specifically for hot stamping] enable weight-saving solutions at a notable cost, because even if the material and the technology is slightly more expensive than conventional products, the decrease of thickness of the material compensates for that.”
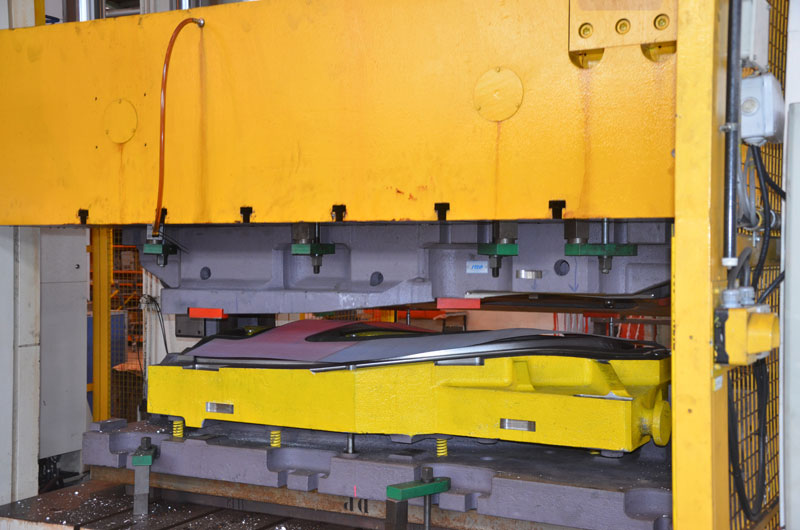
The rise of hot stamping in China
Although hot stamping started life in Europe, it is now being used in almost all major automotive markets. Demand for Usibor in the BRICS varies, says Thirion. “In China, you see the same cars as in Europe. India is a very local market with products adapted for the market.”
The cost-sensitive nature of the Indian market, along with lesser crash and emissions requirements, puts hot stamping lower down the priority list when it comes to investment. “In China, local brands are developing cars to Western standards. In India, the market is far behind. The interest for global standard products is quite low. The market will not develop at the same speed as China. India is much more price-driven than China.”
At a recent media briefing, ArcelorMittal said it expects its upcoming VAMA (Valin ArcelorMittal Automotive) joint venture factory in western China to account for up to 10% of China’s automotive steel production – thanks to growing demand for high grade automotive steel.
ArcelorMittal is forecasting an increase in automotive steel consumption in China from 14 million tonnes in 2012 to 17 million tonnes in 2014, 20 million in 2016, and 22 million in 2018. This demand is due to a growth in annual car sales, which the company expects to reach 31.5 million units in China by 2017.
In China, the demand for Usibor comes mainly from OEMs using it in global platform-based models. “Our objective is to develop the same solutions for China as for other markets…
This is an excerpt from an article first published in the Q3 issue of Megatrends magazine, to continue reading, simply download your free copy and turn to page 59.
Megatrends Q4 will be published in mid-December at awmegatrends.com/emagazines.