The UK government has previously vowed to cut 68% of CO2 emissions by 2030 in a bid to tackle climate change, and announced a ban on gasoline and diesel cars from 2030. It has now gone several steps further with a target to slash CO2 equivalent emissions by 78% by 2035 enshrined in law in April of this year and the sale of new diesel and gasoline HGVs in the UK to be banned from 2040 under the government’s transport decarbonisation plan published on 14 July. To meet these goals, almost half of the UK’s vehicles must be electric by 2030.
The UK is not alone in driving the transition towards EVs—the European Commission’s recently adopted ‘Fit for 55’ legislative package includes revised CO2 vehicle standards, with a 2035 deadline for ending the sale of gasoline and diesel vehicles, and development of the charging infrastructure along the Trans-European Transport Network.
Why might these targets be missed? Low EV adoption.
The main consumer concern is the limited driving range of EVs. Increasing battery capacity is one way to increase the driving range. Alternatively, and preferably, improving vehicle efficiency will mean batteries last longer and EVs can travel further. Vehicles experience resistance from aerodynamic drag, rolling resistance and weight, all of which limit EVs’ range. Polymer composites, including carbon fibre reinforced polymer (or simply carbon fibre), offering lower weight and much greater flexibility in terms of shape than metal, can help to reduce all three.
Attractive automotive applications
Despite the advantages they offer, one of the major challenges in replacing steel structural elements with composites is that the cost of materials and manufacture can be significantly higher. This is particularly pertinent to introducing composites into mass-production vehicles; here cost is of much greater concern than with the few high-performance, low-production-volume vehicles where adoption has been seen so far.
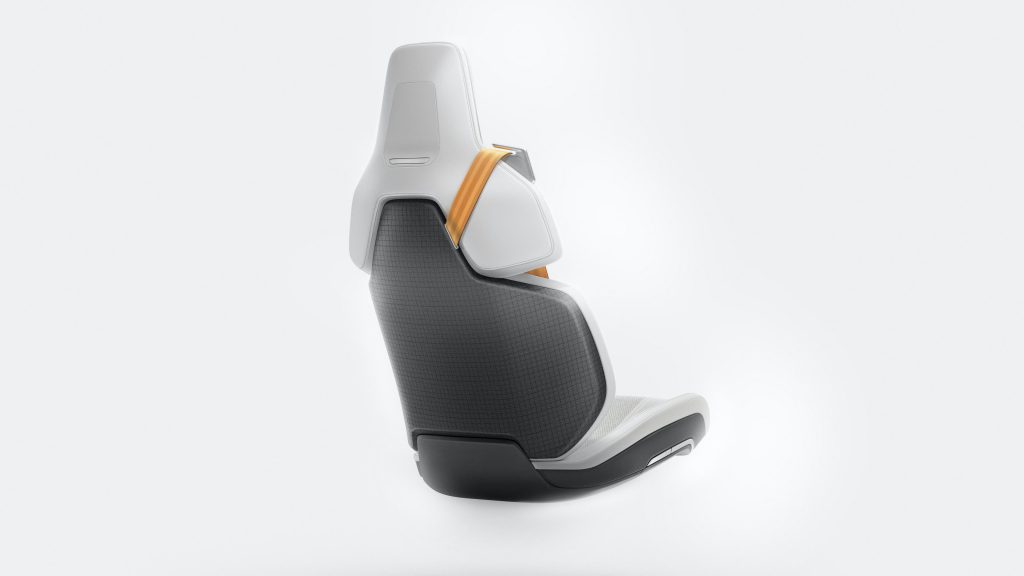
EVs represent an excellent focal point for developing cost-competitive composite solutions: the number of parts that have fundamentally different design requirements and constraints compared to their equivalents in internal combustion engine vehicles, or are completely new, is significant. More radically, the rise of autonomous vehicles will hopefully see us abandon the idea of vehicles being steel boxes with rows of forward-facing seats—new unibody frame shapes will surely arise to take advantage of occupants not needing to face the road or control the vehicle. It’s on this last point that composites have another distinct advantage: the ease of forming radically-shaped structures. This will be a significant advantage with EVs. Aptera Motors’ futuristic-looking solar-powered electric vehicle that recently received US$250m worth of pre-orders has a composite monocoque chassis and uses a raft of other composite structures to provide a vehicle with a highly aerodynamic shape and incredibly low weight. The result: a range of over 1,000 miles—around four times that of vehicles with similar sized battery packs!
The beneficial properties of composites can be exploited to provide vehicles greatly exceeding the capabilities of their steel-centric siblings (and look striking whilst doing it), especially when it comes to EVs
Manufacturing for the masses
Nevertheless, material cost is not the only hurdle for composites to clear. Integration into existing supply chains and production lines is another challenge. Even after identifying a use-case for composites, it can be a major challenge for the component to achieve the required speed-to-market. This is partly because composites have many options when it comes to fibre selection, resin selection, and how these are combined, whereas metals are comparatively simple.
Having optimised the design, manufacture is not straightforward either. Resin transfer moulding, where a dry fibre preform (an assembly of pre-shaped dry fibre layers) is positioned in a mould subsequently injected with resin, is the technology leading the way for mass-manufacture of composites. However, existing solutions currently come with high tooling costs and expertise in using them is not widespread outside the aerospace industry. Both these barriers should diminish as use of composites in the automotive sector grows.
Reduce, reuse, recycle
At the other end of a vehicle’s life lies another challenge: disposal and recycling of composites. This is particularly pressing given the EU directive on end-of-life vehicles requiring 85% of vehicles (by mass) to be re-used or recycled, but is made difficult by the mixture of components in composites. Furthermore, polymer composites are often made from non-renewable resources like petroleum, and fabrication of the synthetic fibres is generally energy intensive. Thus, there has been a considerable push towards developing ‘green composites’ with reduced environmental impact.
Green composites, using natural fibres as the reinforcing agents and/or bio-resins as the polymer matrix, are derived from renewable resources, including low-value agricultural waste, and can be biodegradable. The energy involved in producing green composites can be far less than with traditional composites, so not only are they sustainable but may also have a lower overall environmental impact.
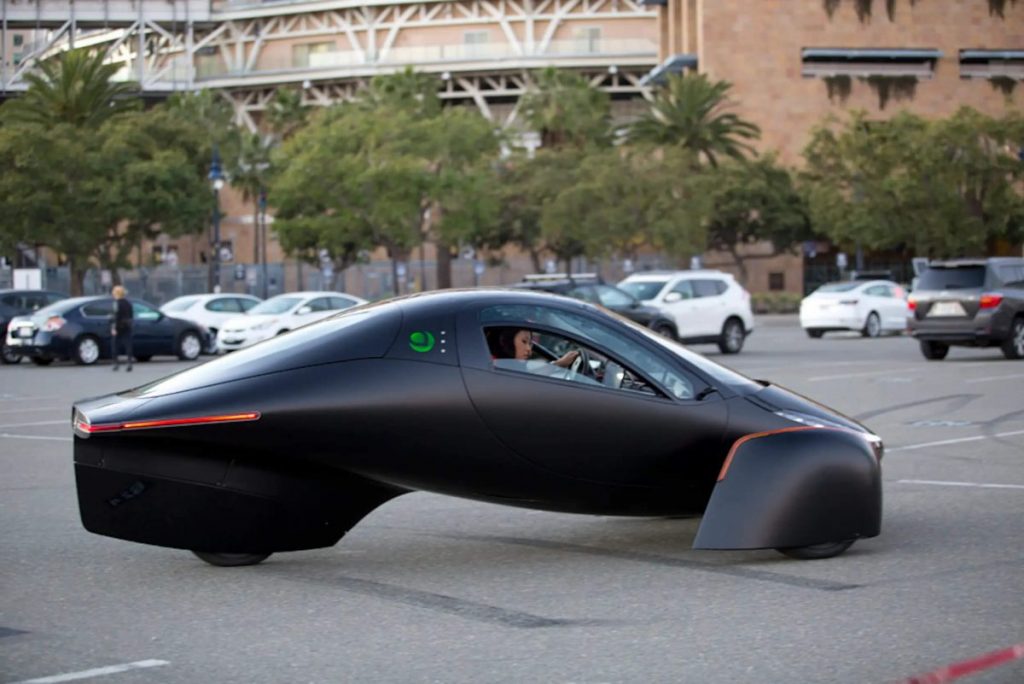
To date, the use of green composites, like other composites, has typically been limited to low production-volume vehicles or for interiors of mass-produced vehicles. However, companies are now focusing on mass-producing sustainable composites for use in all aspects of next-generation vehicles.
Bcomp Ltd. is focusing on producing natural fibre composites on a large scale. The natural fibres used are derived from flax and the final composite can be compression-moulded to form automotive interior panels with up to 70% less plastic and a 50% reduction in weight compared to other composites. The composite also matches the performance of carbon fibre parts, with a CO2 footprint 75% lower. BComp is driving its adoption by collaborating with many large car manufacturers, including Volvo on the XC60 hybrid SUV, and Electric GT on the Tesla Model S P100DL.
Conventional body panels are not the only components using green composites. TRB Lightweight Structures has developed lightweight EV battery enclosures made with a sugar-based resin that is 100% derived from agricultural waste biomass and produced at cost-parity to production from aluminium.
Larger car manufacturers are also moving towards green composites. GM recently filed several patent applications for use of natural fibre composites in interior components of vehicles and Ford is collaborating with Heinz (of ketchup fame) to develop composites made of tomato skins for use in components of future vehicles.
Driving forward
The beneficial properties of composites can be exploited to provide vehicles greatly exceeding the capabilities of their steel-centric siblings (and look striking whilst doing it), especially when it comes to EVs. However, the road ahead is not completely clear. Speed-to-market and manufacturing will continue to present challenges until the inertia of an industry built on metal-based manufacturing is overcome. Further innovation and development in the field of sustainable composites is also essential if the automotive industry is to meet its ambitious sustainability targets.
About the author: Rob Walker is Patent Technical Assistant (Engineering) at Mewburn Ellis