As the automotive world heads towards the next generation of stringent emissions and fuel economy targets, all aspects of the internal combustion engine (ICE) are subject to close scrutiny.
Inherently, ICEs are very inefficient, with efficiency varying between 18 – 40%. This efficiency is a function of friction losses, pumping losses and wasted heat. Currently, automotive OEMs globally are hard at work trying to attack these issues with various solutions to achieve incremental gains.
Engine downsizing
The leading trend is to generate more power from less space, also known as downsizing; this is leading to a reduction in the number of cylinders and a decrease in displacement while maintaining the power output that consumers demand. A secondary reaction to downsizing is the move from a naturally aspirated fleet to a turbocharged fleet. To gain efficiencies and power output, better control systems are a necessity; hence, valve train and fuel delivery systems are heavily controlled and optimised to meet emissions and fuel economy targets.
Let’s consider how powertrain types varied by region. In 2014, gasoline engines accounted for around 87% of the Chinese passenger vehicle powertrain mix, with diesel engines accounting for about 10 to 12.5%. In 2014, 71% of ICEs sold in China had a displacement below 1.6 litres, and 20% of engines sold were between 1.6 – 2.0 litres. In South Korea, 45% of engines sold had a displacement of below 1.4 litres, and 37% of engines sold were between 1.5 – 1.9 litres. In total, 82% of South Korean engines had a displacement below 1.9 litres. In India, about 62% of diesel engines are between 1.0 – 1.6 litres, while that same engine size range accounts for about 48% of gasoline engines. Up to 36% of gasoline engines sold in India are expected to be below 1.0 litre by 2017. The trend in the Asian market is that majority of passenger vehicle engines will be below 1.5 litre displacement after 2020.
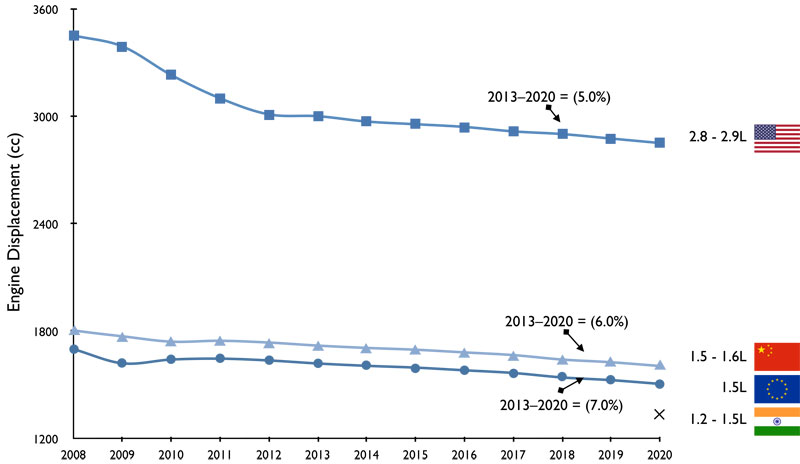
Downsizing will provide consumers with some of the most efficient ICEs the world has ever seen in the mass market. This can also be seen as a trend transitioning ICEs from a primary propulsion source to a secondary power source.
Downsized engines to be turbocharged
There is a correlation between the forecast for engine downsizing and the global sales forecast for turbochargers; as engine displacement falls, turbocharger sales increase to satisfy the customers’ power thirst. This is particularly clear in the global growth forecast for 1.0 – 2.0-litre displacement engines. Global Tier 1 suppliers like Honeywell, Continental, Bosch Mahle Turbo Systems and BorgWarner are aware of this increasing trend and are in the marketplace ready for the OEMs.
Controlling fuel and valve train
Better valve train controls with variable valve timing (VVT) for intake and exhaust valves, variable valve lift (VVL), and direct injection technologies help reduce the wasted heat and pumping losses. Gasoline and diesel engines both have advanced direct injection technologies to optimise combustion efficiency.
The control and durability of the direct injection system provides engineers the dynamic ability to optimise ICEs to meet customers’ needs. There is unquestionably a trend towards ICEs with direct injection regardless of fuel type.
There is a correlation between the forecast for engine downsizing and the global sales forecast for turbochargers; as engine displacement falls, turbocharger sales increase to satisfy the customers’ power thirst
Dual Overhead Cam (DOHC) is the dominant valve train technology today and is expected to continue its domination through 2020. DOHC provides engineers the access to control the intake and exhaust valves far better than SOHC or OHV valve train systems. The growth of DOHC is thus logical and should be expected.
The leading growth in powertrain innovations are ICE downsizing, turbocharging, direct injection and valve train controls. These innovations, when combined, provide the automotive OEMs with a unique set of synergies to reach emission targets, fuel efficiency gains and customer satisfaction.
Powertrain lightweighting
Due to the importance of downsizing, direct injection and other technologies, it is imperative to highlight another key area where OEMs are expanding their limits to gain those extra few kilometres per litre of fuel: weight reduction. From an emissions perspective, it is estimated that every 50kg of weight reduced from an average 1,500kg vehicle cuts CO2 emissions by 4-5 grams. Frost & Sullivan studies indicate that a vehicle with an average weight of 1,500kg has the potential to lose up to 35% of its weight by 2020, consequently causing powertrains to be about 8% lighter than existing offerings.
The key areas of the powertrain on which OEMs will focus their weight reduction efforts will be engine, transmission, exhaust, fuel system, casing, batteries and motors. Studies reveal that it is possible to reduce about 100kg in the medium term, enabling savings of about 8g CO2. The key drift in material technology is likely to happen with heavier engine components like cradles, engine blocks, cylinder heads and gears. While engines will constitute of an increasing level of advanced high strength steel (AHSS), aluminium and magnesium, some steel-based transmission parts are likely to shift towards the use of polyamides (PA); both cases offer weight reduction possibilities of up to 40% in the medium term.
The key to OEM lightweighting strategies is targeting the right application for the right segment. While larger segments have the price cushion to pass on compliance cost to owners, mid-sized cars will have moderate compliance costs that will impact purchasing decisions if passed on to buyers. Smaller segments have price sensitive buyers, but the relative compliance costs are also less impactful.
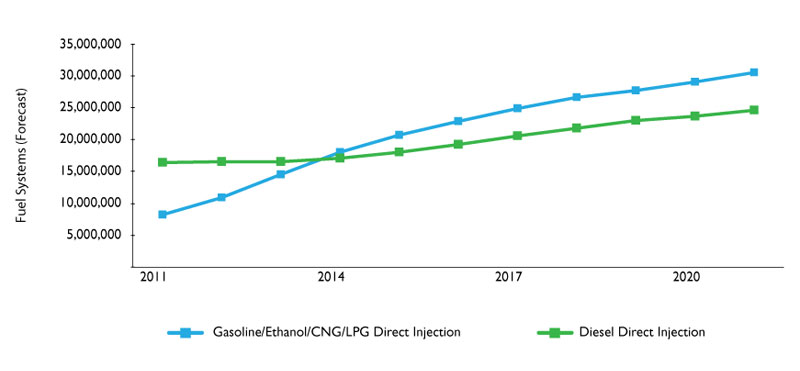
Innovations in noise, vibration and harshness
Engine innovations such as stop-start systems, hybrid and plug-in hybrid technology, cylinder deactivation and turbocharging technologies increase the NVH (noise, vibration and harshness) challenges on a vehicle, due to the variations in the layout and transfer path. Such challenges have led to innovations in engine mount and noise cancellation technologies.
Honda was one of the first OEMs to commercialise mass-market active control engine mounts in its cylinder-deactivated V6 engines. Led by the German OEMs, the vehicle manufacturers in Europe are adopting sophisticated active mounts on premium vehicles. Audi and Porsche have fitted unique and sophisticated electromagnetic oscillating coil and magneto-rheological engine mounts respectively on the Audi S8 and Porsche 911. These vehicles also come with active noise cancellation which counteracts unwanted noise through destructive interference, thus almost eliminating any airborne noise from the vehicle. The epitome of innovation is within the active exhaust system, where microphones are installed on the exhaust to absorb unwanted frequencies, and speakers produce characteristic sound. The speakers can be tuned to produce an authentic signature sound; the vehicle’s engine sound can be changed according to the driver’s mood or the vehicle’s mode. A system developed by exhaust sound engineers from Eberspächer is currently being tested in Europe.
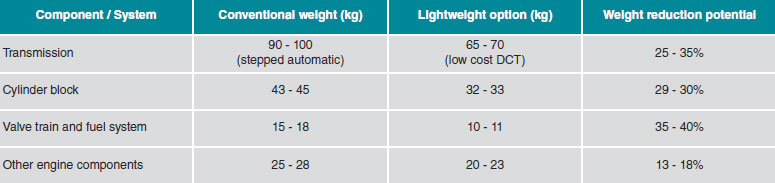
Beyond Euro 7 – exhaust gas heat recovery innovations
On average, two thirds of the fuel energy is wasted through the exhaust gases and the cooling liquid. In order to minimise fuel consumption and engine emissions, the conversion of exhaust heat energy shows great potential. Wasted heat can be utilised indirectly for power generation using a Rankine cycle, or directly for thermoelectric generation.
A thermoelectric generator (TEG) converts heat directly into electricity in a simple and reliable way, known as the Seebeck Effect. Currently, various integration configurations are being evaluated and 200-1000W energy recoveries have been achieved. Cost and technology infancy are the major barriers for TEGs. OEMs such as BMW and Ford are leading development programs, with the former likely to be the first to commercialise this technology closer to 2020. Fuel economy gains of 3 – 7% are achievable through TEG systems.
An indirect method of exhaust heat recovery using the Rankine cycle is based on the steam generation in a secondary circuit using the exhaust gas thermal energy to produce additional power by means of a steam expander. A Rankine cycle engine makes only minimal impact on the engine pumping losses when compared with turbo-compounding. Also, with respect to a TEG, a Rankine cycle engine provides higher efficiency of heat recovery. However, cost, weight and reliability are major challenges for Rankine cycle recovery systems, and are unlikely to be commercialised before 2020. Although BMW and Ford have demonstrated Rankine cycle engine concepts, Honda is one of the OEMs looking to pursue Rankine cycle technology for hybrid applications in production vehicles. Vehicle power output can be boosted by about 10 – 15% using Rankine cycle engines.
Alongside energy recuperation, exhaust heat recovery (EHR) systems are considered as one of the key energy recovery technologies preferred by OEMs as we head towards 2020.
Sujeesh Kurup and Anjan Hemanth Kumar