The realisation of software-defined vehicles (SDVs) will require a radical reassessment of vehicle design and production. Designing vehicle software can be expensive and time-consuming, and major automakers are generally inexperienced in the field. The issue is also compounded by the need to continuously provide over-the-air updates in a timely manner.
To ensure they can realise SDVs without incurring hefty costs and delays, automakers will need to embrace technologies that can streamline processes wherever possible. Digital twins are among the more notable developments in this regard, capable of simulating everything from individual vehicle components to entire factories. Their use can allow for more detailed experimentation, shorter development cycles, and minimise the need for physical prototypes and processes.
Virtual proving grounds, a detailed replica of the real-world vehicle testing environment, are among the more promising types of digital twin available to automakers. Historically, physical testing has dominated vehicle development, but automotive software firm VI-grade believes this is increasingly unnecessary. To this end, the company has developed a range of virtual proving grounds that serve as replicas of real-world locations. By using these simulations to deliver “laboratory-like” accuracy, it believes it can accelerate software development by eliminating the need for the majority of physical testing scenarios.
The virtual option
Guido Bairati, Managing Director of VI-grade believes that digital twins will be crucial for SDV development. However, that potential must be maximised by accompanying them with a range of stress test tools. “Once you have twinned the vehicle, the next challenge is to simulate different events in the same manner as a real physical prototype,” he tells Automotive World. “For this, we need a digital proving ground.”
VI-grade’s virtual proving grounds are used in its proprietary VI-WorldSim, a digital environment that can accommodate a range of scenarios. It provides a modern, lifelike replica of real-world conditions in terms of visual fidelity and physics simulation. By running a proving ground scenario inside this simulator, engineers can test prototype vehicle architectures, software functionalities and updates in a manner that “comes close to driving a real vehicle”, according to VI-grade. Since launching its proving ground programme in July 2024, the company has created eight digital replicas of real-world testing sites, including the Colmis Proving Ground in northern Sweden and the Nardò Porsche Technical Center in southern Italy.
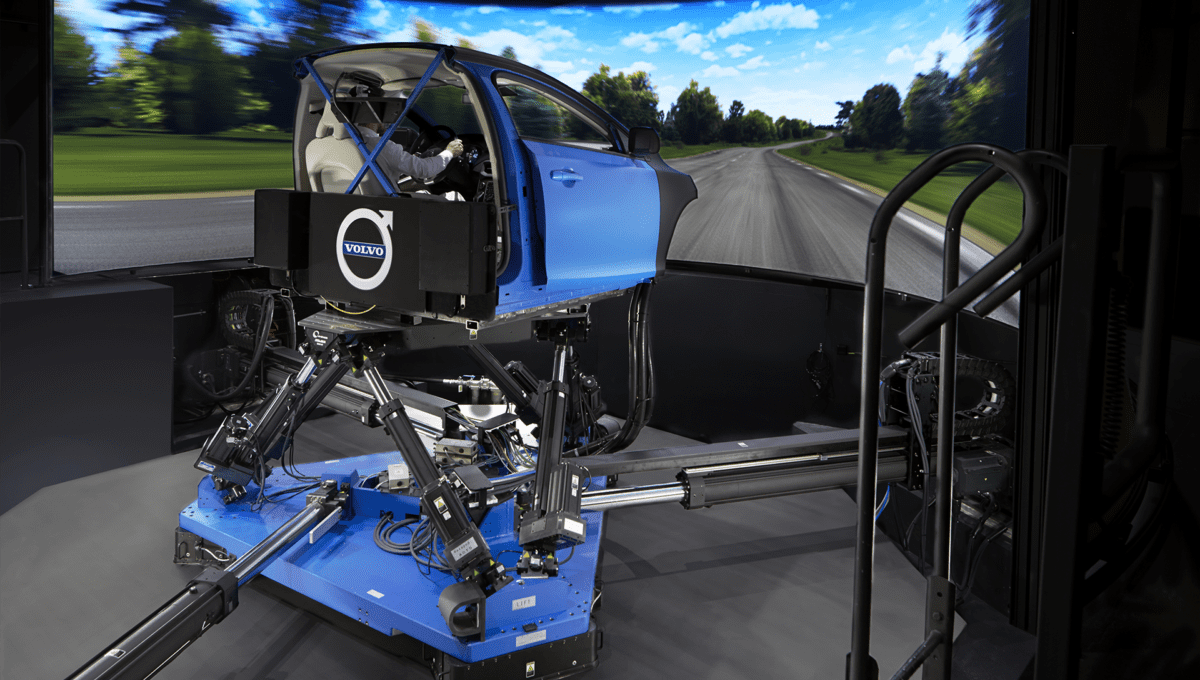
“With a virtual proving ground, you can do a lot of testing without leaving your laboratory. You don’t have to ship physical prototypes, engineers and drivers around the world to test different conditions,” remarks Bairati. This saves a substantial amount of time and money, while also eliminating a great deal of busywork. He adds that there are issues exclusive to real-world testing, such as the restriction of extreme winter testing to only a few weeks per year, during which time physical proving grounds have to contend with many bookings from different clients. “If you want to do winter testing for, say, braking software, you can do this with a simple mouse click.”
Accuracy is key
Bairati notes that VI-grade’s virtual proving grounds have been used to trial a variety of software, primarily advanced driver assistance systems. However, it can also be used to test a wide variety of software governing the control of a vehicle, including anti-lock braking systems, electronic stability programmes, and engine control modules.
Testing can quickly result in the generation of a “vast” amount of data —more than can be reasonably accomplished in a physical environment—which could then be used to further refine the software. However, the reliability of the data depends on the accuracy of the vehicle prototype digital twin. “That’s step one. Step two is to have an accurate proving ground and testing conditions,” says Bairati. While VI-grade is confident in the fidelity of the WorldSim’s physics, it is crucial for automakers to reciprocate with an accurate digital replica of the vehicle or feature in question.
For its part, VI-grade offers a range of tools to enrich the reliability, range, and quality of data generated in digital environments. For example, its actuator-based DiM Dynamic Simulator—a physical vehicle simulator—can be plugged into the world simulator to “bridge the gap between testing and simulation”. The automaker can slot its own chassis into the physical simulator to test its responses to the digital environment. As the digitally twinned vehicle navigates the virtual proving ground, it responds accordingly: turning at a corner, tilting on an incline, etc. The resulting data generated can be used to further improve the accuracy of the vehicle’s digital twin, as well as improve the resulting vehicle.
Changing mindsets
The combined use of VI-grade’s simulation tools opens up possibilities that are generally not feasible in real-world testing scenarios, particularly edge cases where testing with a human driver could put a life at risk. “Some things are simply too dangerous to replicate in the real world,” remarks Bairati. “Simulation offers a safer way to test an SDV in these cases.”
Some things are simply too dangerous to replicate in the real world
He estimates that up to 90% of all vehicle testing could be accomplished using a simulator, particularly as softwarisation takes on an increasingly prominent role in vehicle development. “A lot of our customers tell us that they are just doing the final tuning at a physical proving ground.” However, many remain sceptical of trusting the results of a simulation. As with the automotive industry’s transition towards software in general, Bairati posits that an unwillingness to embrace new mindsets is holding back the technology’s full potential.
“There are still companies that believe real physical prototypes give better feedback than virtual models. They might be right for some aspects of vehicle design, but the gap between virtual and physical is getting smaller every day,” he concludes. Given the cost- and time-intensive nature of modern automotive software development, a mindset shift may be necessary for some OEMs to achieve their SDV ambitions.