With automotive manufacturers such as Nissan planning to sell at least one million electric vehicles (EV) annually by 2022, and Audi set to reach 800,000 by 2025, it is clear that electrification is gathering momentum in the mobility sector. EVs are projected to account for 19% of the market by 2030—with battery electric and plug-in hybrids accounting for 11% and internal combustion engine (ICE) only and mild hybrid vehicles the remaining 70%. Many new models will see the light of the day very soon, making the entire supply chain work together to address production challenges and consumer scepticism.
New component requirements
In terms of development, moving away from the comfort zone of the ICE can be a daunting prospect, particularly as the requirements at a component level can be entirely different for electric or hybrid vehicles. Because of the inevitable increase in electrical components, the need for thermoplastic, TPE and liquid silicone parts is greatly increased, as well as multicomponent parts for electronic control unit housings, for example, and power connectors with integrated connector pins. Many also require special properties—such as electrical or thermal conductivity—and sealing solutions in particular are adapting rapidly to become intelligent in terms of their functionality.
A perfect example of this can be found in sensor technology, which will be prevalent in EVs due to its natural affinity with the power source. By using smart sealing solutions with sensors embedded, not only can you ensure the integrity of the seal, you can also add the ability to monitor a wide range of activities within the vehicle. An integrated sensor could monitor or track functionality, for example, or other elements such as temperature, humidity or leakage, delivering data to the vehicle itself or to the manufacturer or driver.
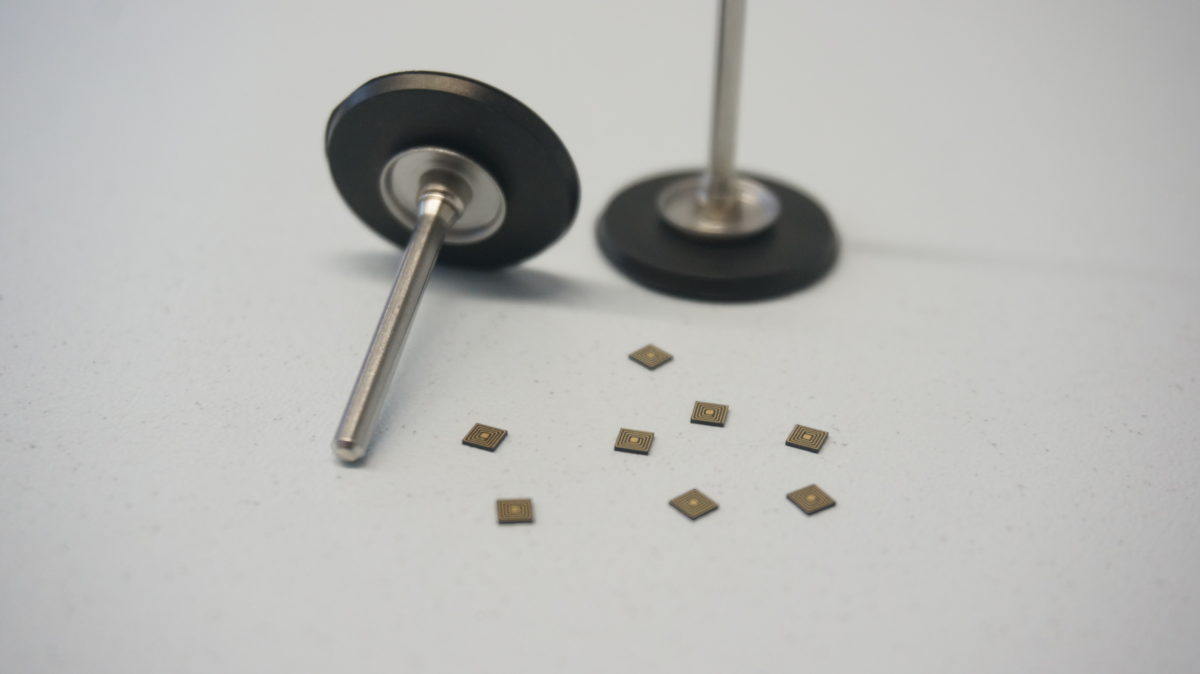
Predictive maintenance and predictive analytics will also be possible, as the sensors within certain seals will be able to detect whether parts are wearing or are close to failure, ensuring their replacement can be scheduled before such an event leads to unscheduled downtime of the vehicle or even potential safety issues. This active data will be key to realising the full potential of sensor technology, even to the point of monitoring certain elements of driver behaviour.
Of course this is just one example of many where intelligent sealing solutions can be deployed in EVs. To take another key example, these new technologies will require far more housings than standard ICE alternatives, and integrated sealing solutions can provide significant benefits in terms of added functionality. Where control electronics are concerned, for example, features include thermal conductivity, EMI shielding and the stabilisation of conditions within the housing itself.
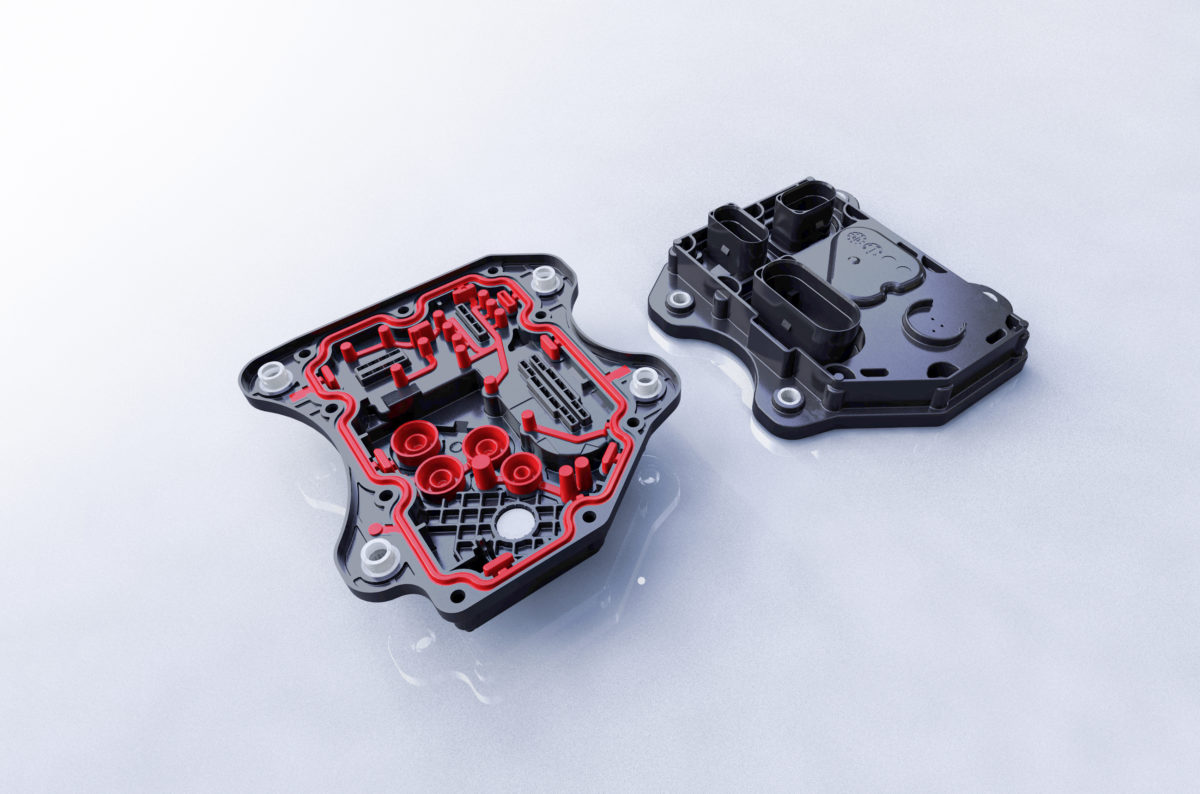
Manufacturer/supplier relations are changing
This trend towards greater functionality is driving a paradigm shift in how manufacturers and components suppliers work together, and indeed how they will work together in the future. For both existing manufacturers and those looking to enter the EV market, the way in which sealing solutions assimilate into designs will be more important than ever before.
The key is to engage with co-engineering partners at an early stage, as the competitive advantages of doing so can be highly appealing—provided the chosen components supplier has the capabilities to deliver. For example, historically the development of a sealing solution would be a very iterative process. A prototype would be created, tested, modified and tested again until the correct outcome was achieved.
Today, with advanced simulation capabilities available, product development time can be shortened and therefore time-to-market and cost can be reduced. Through working closely with manufacturers from the outset, designs can be optimised in terms of the sealing elements to ensure there are no unforeseen issues when a product goes into full production. This can even include the simulation of the flow behaviour of the compound—how it will behave when injected into a mould cavity, for example—and how the gating system can be designed to optimise the required tooling to ensure the most efficient production processes for manufacturing the highest quality products. Every design and processing detail can be simulated and checked ahead of time, meaning manufacturers can enter into production with the full confidence required of their sealing solutions.
Material knowledge and design know-how are paramount
The creation of advanced sealing solutions for unique and customised applications requires compounds that are tailor made for purpose. Here, bringing efficient solutions to the table that perfectly meet the requirements of sophisticated and novel products and applications is key, particularly as electrification is bringing some new requirements on materials used in EVs.
Accurate virtual models are the prerequisite for FE-based simulation techniques and the precise knowledge of material behaviour is key for realistic predictions of component performance. Generic material parameters available for simulation models are often just based on the material hardness and are not close enough to produce accurate simulations in the first instance, and must be honed in order to be viable—which of course takes time.
The solution is to ensure the parameters of the material models can be determined as close to reality as possible from the outset, which accelerates the product development process still further. Additionally, these material models can be shared with customers for their own simulations, which provides them with a further competitive advantage.
The combination of tailored materials with optimised designs is the key for providing outstanding product solutions. Furthermore, sealing systems will only achieve their optimum functionality if the designs of the sealing element and mounting space are a perfect match. The components often have a system-critical or success-critical role, therefore it is paramount to invest sufficient time and resources in the proper development and engineering processes at the correct point.
Successful co-engineering projects require cooperation very early in the development process, when there is still sufficient design freedom for the overall system to optimise both the sealing element and the installation space. This mitigates the risk of having to reverse engineer or, worse, redesign a part to accommodate the sealing element. Ultimately, it is best to engineer a solution that is integral to a design, rather than to engineer one to fit into a design retrospectively.
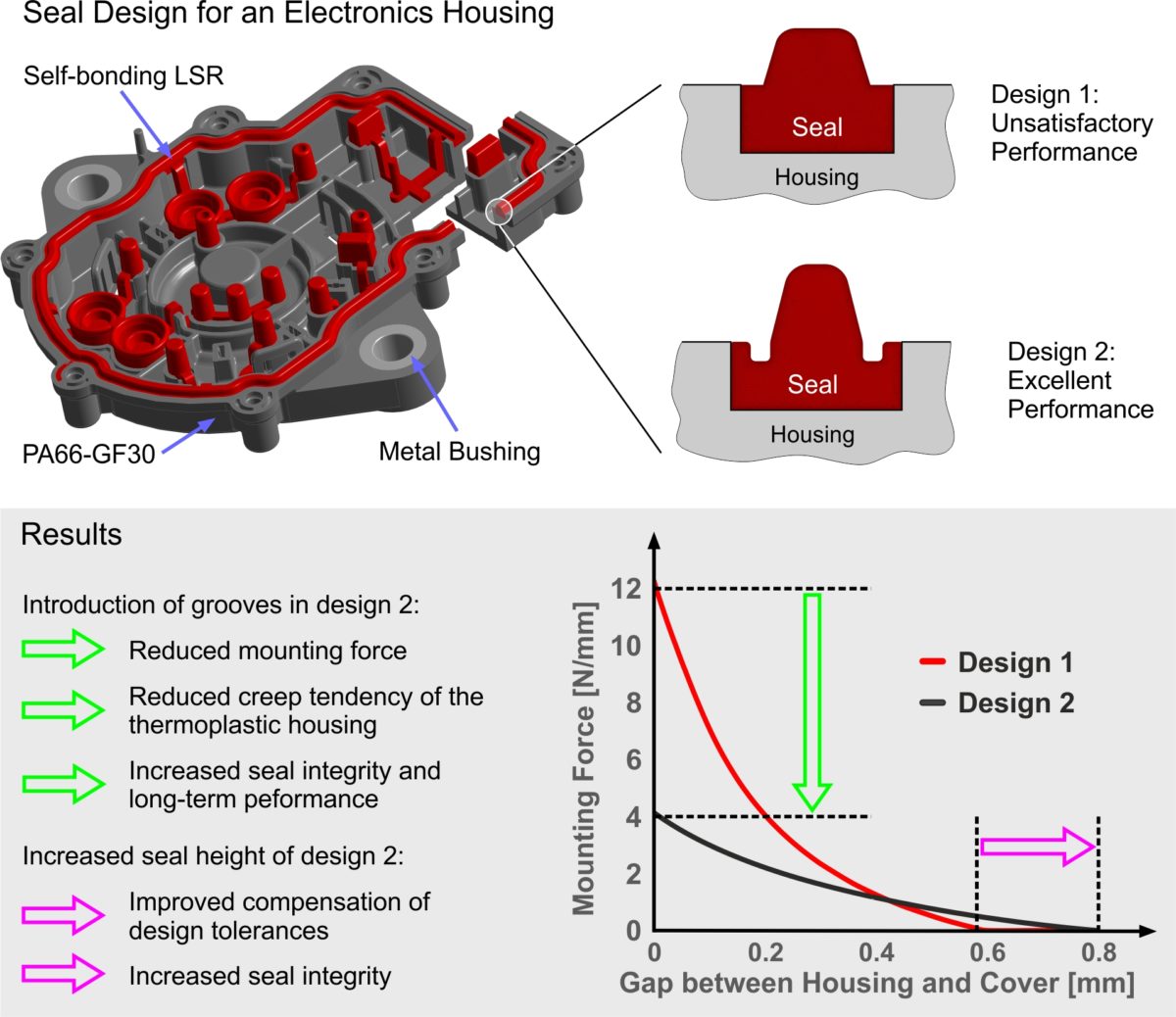
The mobility sector is advancing rapidly, and the electrification of vehicles of all types is an inevitability that manufacturers must address to safeguard the future of their business. However quickly full electrification is achieved, the fact remains that components used for the technologies of today and the future are more sophisticated than ever, and as the sector evolves, so too must the materials used to build them and the processes adopted to optimise their performance. Engaging with expert suppliers is crucial. The key is to do so as early as possible in the journey.
About the author: Andreas Minatti is Head of Business Development at Datwyler, a provider of system-critical polymer components