Low carbon has become a hot topic within the automotive industry, primarily from the consumer perspective of tailpipe emissions. This concern has been powering interest and investment in electric vehicles (EVs), but it only represents half of the picture. Manufacturers and suppliers are increasingly addressing the carbon footprint of what goes into a vehicle and how that vehicle is produced.
MobilityScience
Materials expert Dow is at the fore of this movement, actively supporting automakers and their suppliers in the journey to deliver a lower carbon vehicle. In 2020 Dow launched MobilityScience specifically to help transportation companies with sustainable materials innovation.
Specflex C is a case in point—Dow launched this lower carbon urethane material made from automotive waste in 2021, targeted for use in applications like vehicle seating foam. It promises the same light weight and geometrical adaptability as current automotive polyurethane foams but at a significantly lower cradle-to-gate carbon footprint.
“We are taking a waste stream out of the automotive industry, depolymerising it, converting it back into virgin materials, and then selling it to companies as a circular lower carbon polyurethane foam,” explains Dow’s Tim Boven, MobilityScience Vice President.
Another key contribution comes in the form of adhesives that cure quickly or at room temperature. Adhesive technology is used extensively within the automotive industry but frequently requires high temperatures for curing, meaning more production emissions and energy use. Dow’s room temperature cure materials avoid this issue, therefore cutting the OEM’s omission profile within production.
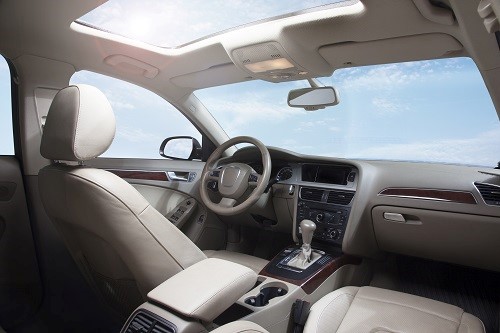
Recyclable self-sealing tyre technology is another innovation supporting the low-carbon car. Self-sealing technology automatically repairs tyre punctures and eliminates the need to carry a heavy spare tyre in the boot at all times. The trouble is that traditional sealing material has caused problems for recycling. “It gums up the system,” Boven notes. In collaboration with Bridgestone, Dow recently introduced a self-sealing solution that is easily removable when the tyre is recycled. “This means it doesn’t disrupt the recycling system, yet still allows an OEM to eliminate that spare tyre. That’s important because tyres are heavy,” he tells Automotive World. “This is all about lightweighting the vehicle. Kilos matter, so when you can remove a tyre it’s a significant contribution.”
Clean comes at a cost
Dow has poured money and manpower into these innovations, and will need to recoup that investment. So will every other developer out there. What does that mean for the cost of low-carbon technology for the consumer and the market at large?
Boven believes it entails a near-term price premium but only a temporary one. “Low-carbon product technology is more expensive today because of the investment that’s needed largely in the infrastructure and the capital footprint to recover those materials, to break them down and to put them back into the system,” he elaborates. “We’re very early in the innovation cycle for advanced recycling techniques. In some cases the price tag is higher to offset the capital investment and the infrastructure that has to go into it.“
Recycling often has a higher carbon footprint than the virgin material
At the same time, activity on the policy front could change the economic equation of these materials. “Policies like EPR (Extended Producer Responsibility) schemes and fees for recycling can either accelerate some of this or slow it down,” he adds. “Policymakers could become more aggressive, like we see with the end-of-life vehicle directives, and mandate much higher recycled content for vehicles in Europe. If that policy starts to disseminate around the world, we will see this push accelerated. If we’re waiting only on market forces, as they exist today, it will mean a longer time horizon.”
How low can we go?
The coming years will hopefully see steady progression towards low-carbon transport. EV sales are projected to accelerate, with some forecasts calling for a 50% penetration rate within the US new vehicle market by 2030 and a 67% penetration rate in Europe. Many of these EVs will feature innovative low-carbon solutions from Dow and its competitors. But there are still some challenges ahead to realising this green vision.
One of Boven’s focus areas will be to make sure these eco-friendly materials do not impede end-of-life vehicle recycling. He points specifically to adhesives as an example: “Consider an adhesive put on a metal substrate. How can we ensure that the adhesive doesn’t inhibit the recovery or disassembly of that metal? How do we take spent polymers, depolymerise them and introduce those back into new vehicles?”
The key is to offer circularity that has a lower carbon footprint. “Those two things don’t necessarily go hand in glove,” he emphasises. “Recycling often has a higher carbon footprint than the virgin material, simply because of the recovery and transport of the material, as well as the processes required to break it down.” All of those have a carbon footprint in and of themselves.
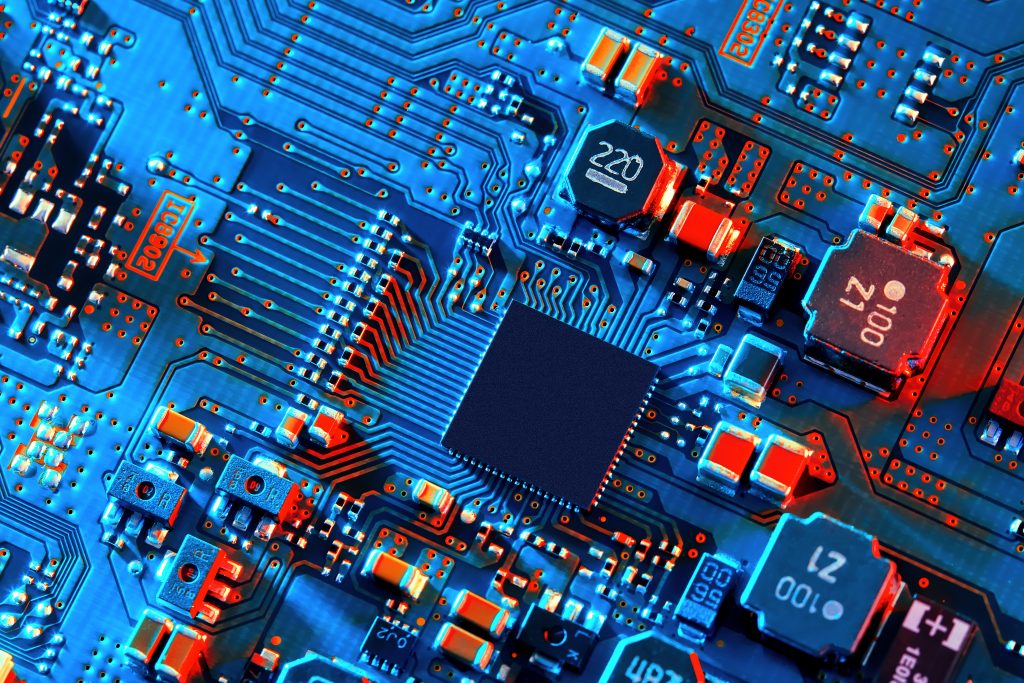
Virgin plastic, for instance, has a low carbon footprint but poses significant challenges for recovery and recycling. The qualities that make it so appealing—durability, functionality, long-lasting—are the same aspects that make it hard to recycle. If the carbon footprint of recycling is higher than the virgin material, circularity by itself may not in fact be better for the environment. Dow is pointedly working to drive more circular solutions that are indeed lower carbon for future vehicles, and is drawing on its reach within numerous industries. For instance, it is leveraging tech developments within food packaging recycling and applying it to automotive. Similarly, the adhesive and thermal management materials that it has been developing for consumer electronics can be brought into the booming automotive electronics sector.
A convergence of sectors
This wide breadth of industry participation could give it a real edge moving forward, as Boven sees “the future of low-carbon transportation as a collision of these market verticals.” He elaborates, “You have to be conscious of what’s happening in the hydrocarbon and energy markets and the consumer electronic markets because all of that is coming into automotive. Historically, these were siloed, but there is a convergence here with the future of mobility.”