In the period between now and 2020, the automotive industry is expecting to see considerable change in the use of plastics in automotive applications. A study published by Grand View Research shows powertrain applications as the fastest growth area for automotive plastics during this period, with a forecast CAGR of 10.4%. Overall, says the report, global automotive plastics demand is expected to reach 14,851 kilotonnes by 2020.
DSM Engineering Plastics, headquartered in the Netherlands, has been working with the automotive industry to design lighter, safer and greener components. Megatrends asked Bob Akins, the company’s Vice President – Marketing & Sales, and Glenn Cannavo, Automotive OEM Manager, about the capabilities of plastics in automotive under-the-hood applications.
The use of plastics in automotive powertrain applications is set to enjoy considerable growth over the next few years. What lies behind this growth?
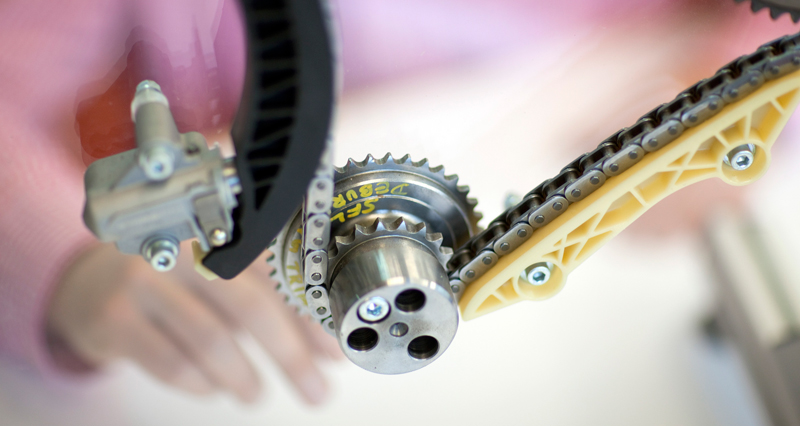
Overall, the plastics segment in powertrain is a growth segment, based on the need to improve fuel efficiency and reduce mass. Our high temperature materials, and our high friction materials were what initially led us to focus on powertrain.
One of the key issues in powertrain is chemical resistance, which is what all our products deliver. Our customers are looking for applications at 150 degrees Celsius, on a continuous basis. If you look at our product line, we fit that space. And we know that they’re increasing that requirement as well, approaching, in some cases, up to 200 degrees Celsius. Our whole product line of nylon and polyesters fits there very well.
What are some of the ways in which plastics can deliver fuel savings in the powertrain segment?
Well, the driver for fuel economy is taking out mass, which means less moment of inertia. One of the ways of doing this is to take out mass and replace steel or aluminium with a plastic. Additionally, we look at friction reduction. A low coefficient of friction means less inertia is required to move something. Those are two key areas for us.
In addition to fuel economy, another key area is manufacturing. The secondary operations required for machining steel or aluminium are costly compared to manufacturing plastic.
You also talk about cost reduction. How does a vehicle manufacturer save costs when using plastics in the powertrain segment?
We can simplify the cost of manufacturing components, which is probably what first led to the use of plastic in the automotive industry. Take, for example, an air intake manifold that’s cast, machined, and then polished. Many smaller, dimensionally critical components are machined. You can take a piece of aluminium and its material cost is acceptable, but it takes considerable machining – and additional cost – to convert it into a component. We can mould those shapes in plastic without the secondary operations. And this also reduces the number of components. We can consolidate, we can design in complexity and we can eliminate part numbers.
How do plastics compare with other materials in a total lifecycle analysis?
If you look at the whole lifecycle analysis, the amount of energy it takes to produce plastics is one area. We also look at the recyclability, what plastics can be reclaimed and reused, what really is being retained and reused, and the savings over the life of the vehicle. Our analysis shows that the energy cost that could come in higher for plastics is reclaimed during the life of the automobile and the savings that you see in that area.
Can recycled plastics be put back into powertrain products?
Usually, recycled plastics would go into other products. Recyclability depends how well the overall system is set up for recycling. Moving forward, one of the main drivers to make things more recyclable is having the ability to reclaim components. Once reclaimed, there are many avenues you can take them to be used in other applications. But to have the ability to reclaim them to begin with is where the big challenges lie.
Looking to the future, where do you see the automotive plastics market heading? Where are the growth areas?
From our standpoint, the big growth areas include the powertrain and vehicle electrification; not only electric vehicles themselves, but the many components in the car that are moving to electrically-driven applications. Those are two of the big areas that we continue to focus on, moving forwards.
If you look at engine components, there are certain places where you can take out mass that we’re looking at. Engine downsizing and turbocharging are improving fuel economy. Traditionally, those systems were low volume and used a lot of stainless steel. Plastic materials are replacing some of those stainless steel parts as volumes increase. So they’re making engines smaller, but some of the components will also switch from stainless steel to plastic composite materials.
We’re also working on safety applications. There are several areas in the airbag system where we can use different plastics. Typically these have been metal in the past, but we’ve been able to convert them to thermoplastics.
David Isaiah