Many manufacturers in the automotive space struggle with rejected and scrap material when producing complex parts. New grades of steel have been developed with what is known as ‘high edge ductility’ as part of an effort to improve the quality of cut edges, and to facilitate more complex components without increasing material thickness and weight.
The ever-present trend of lightweighting places high demands on any manufacturer and its suppliers, and has been a core driver in developing higher strength materials. One approach to lightweighting is to simply use less material. However, by reducing thickness, costs can soar as more exotic materials become necessary to retain strength.
According to Nordic steel specialist SSAB, steel is “clearly” the material of choice when it comes to cost efficient weight reduction. Today, grades of advanced high-strength steel (AHSS) and ultra high-strength steel (UHSS) sit at around €5 per kilogram of weight saved (US$5.68/kg). For aluminium, it is around €12/kg; €15/kg for magnesium and €25/kg for carbon fibre reinforced plastic (CFRP). While steel can offer a significant saving, producing complex parts that are strong, light and without defects can be a challenge.
Strong and formable
Generally speaking, the stronger the grade of steel is, the lower its elongation value — the material is simply harder to work with and form. The challenge, according to Daniel Sund, Product Manager at SSAB, is that because lightweight parts are thinner, more complex shapes are required to fully utilise the material’s high strength and to avoid buckling.
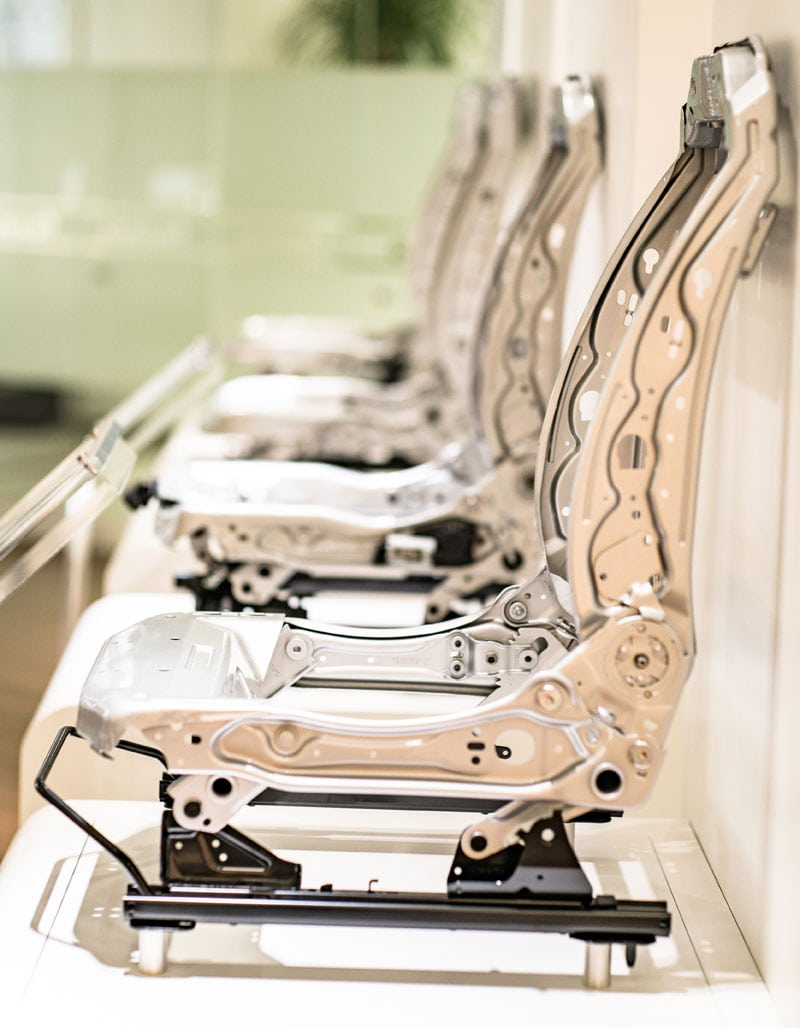
Alongside the pursuit of stronger steel, producers are also improving the formability of existing grades. The elongation values — an indication of ductility — that can be achieved with such ‘third generation’ steels are “really promising,” said Sund during a recent Automotive World webinar. “However, looking at the elongation value only as a means of describing formability may be a bit misleading.”
As he explained, there are several different elements to take into account, such as ‘edge ductility’. When an AHSS part is cut mechanically, the edge of the material at the cut can deform and suffer from issues such as ‘micro cracks’. This led SSAB to develop DOCOL HE, an automotive grade high-strength steel that is purpose built for high edge ductility. It can allow for strong, light and complex parts, with a significant improvement to the quality of cut edges.
“When we work with high strength steels we may not have cracks in the part itself, but we might sometimes have issues with its edges,” said Peter Alm, Senior Forming Expert, SSAB. “This is why we have developed this new HE grade.”
It has an extremely fine micro-structure compared to standard MC/LA grade steels available today. Visually, the edge of a cut DOCOL HE part is significantly cleaner when compared to that of traditional high strength steels, which can appear rough at the edges. At a mechanical level, those defects can have potentially severe implications to the quality and performance of the part as a whole. Rejection is a common result.
“DOCOL HE offers improved cut edge quality and edge ductility. When you combine these things you also achieve an improved hole expansion performance,” explained Alm. Generally speaking, a material’s hole expansion reading decreases as tensile strength increases. As such, a low hole expansion value denotes a stronger material. Bendability and local formability is also improved — characteristics which generally reduce the chance of material failure at cut edges.
More advanced designs
SSAB believes that this new form of steel could prove particularly useful in the production of vehicle parts that have a collar or a stretch flange, a common feature of stamped parts in order to increase stiffness.
Consider a suspension control arm, for example, or other complex mechanisms. DOCOL HE is also well suited to producing other chassis, seating and powertrain components, advised Alm: “This material would really help with these kinds of parts, thanks to the benefit of being able to make more advanced designs.”
Then there are the benefits in terms of tooling, with reduced wear and less sensitive tool settings required. “Customers can run longer sequences before they need to stop the production line,” explained Sund.
While the push for ever-stronger steels will continue, those with high edge ductility are expected to improve productivity and competitiveness without sacrificing strength.