Fiat’s recently revived automotive production plant in Serbia has attracted new investment in the region from DB Schenker Logistics. The logistics specialist, headquartered in Germany, has opened a new warehouse in Kragujevac, just 7km from Fiat’s vehicle production facility. DB Schenker’s new warehouse will specialise in providing logistics services for suppliers to Fiat’s nearby plant.
Fiat reopened the Kragujevac plant in April 2012, revamping a site previously occupied by state-owned manufacturer Zastava. The plant currently builds just one model, the 500L MPV, with capacity for up to 180,000 units a year. Last year it rolled out around 30,000 500L units. This year, the first full year of operation, production should soar to 160,000 units. Fiat also plans to add new models and expand exports to numerous markets.
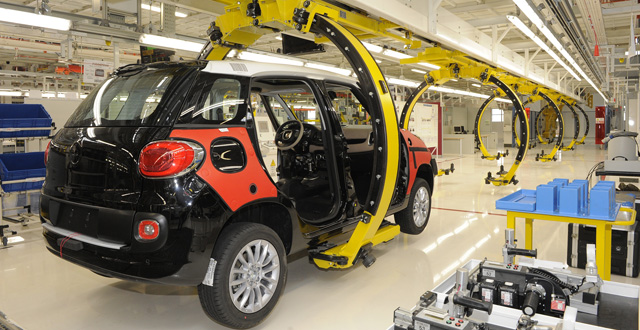
DB Schenker has described the new warehouse as “another important step in strengthening its service portfolio in Serbia.” Its first customer is AGC Automotive Europe, a supplier of glass components. AGC Automotive Europe is also working with DB Schenker in Slovakia for component deliveries to Hyundai/Kia and in Germany (Bremen) for deliveries to Daimler.
The new logistics plant in Kragujevac is classified as a bonded warehouse, connected to Fiat’s free trade zone. The facility has implemented DB Schenker’s own production supply system, developed specifically for supplier projects in the automotive industry. The glass components of AGC Automotive Europe are stored in the warehouse and then shuttled to the plant just in time according to the production demand. DB Schenker offers an EDI data flow for AGC in this project.
“The partnership between DB Schenker and AGC in Serbia became a successful story thanks to a strong co-operation between both parties, in a particularly difficult project,” comments Luc Tassignon, European Logistics Flows Coordinator of AGC. Only six months before starting the operations, the decision was taken to open a sub-contracted warehouse. Despite the very short period, we achieved unexpectedly good results on objectives in a very complete project with customs clearance topics, warehousing, EDI links and re-deliveries to Fiat.”
So far, AGC is the warehouse’s only customer, though it has space for other automotive suppliers to the Fiat plant. Neven Marcesku, Managing Director of Schenker d.o.o., Belgrade, expressed his confidence in attracting new customers in the Kragujevac region and added: “Contract logistics is an attractive growth market and the new business with a customer like AGC Automotive Europe is very important for us. It’s not only confirmation of our global strategy in the field of automotive logistics but also confirmation of our active approach to the Serbian logistics market.”
However, the potential for growth at Fiat may be hampered by the OEM’s supplier park. Fiat’s local site includes a supplier park that houses eight major suppliers of the plant’s main components, all within 2km of the vehicle assembly facility. The site includes facilities operated by Johnson Controls for the dashboard, and Dräxlmaier, which produces the cabling. Seats, wheels, door panels, headlining, sunroof, glass and more than 120 plastic components are all produced on the site by a number of suppliers.
Part of this move was due to the harsh winter weather seen in Serbia, which can disrupt the transport of key parts. Speaking to Automotive World last year, Fiat Automobile Serbia Chairman and Chief Executive Antonio Ferrara explained: “We planned this from the beginning, particularly since winter conditions are completely different to those in Italy.”
Logistics supplies may also be hampered by poor road conditions. Last year Fiat complained that several infrastructure projects promised by the government, in particular access roads, had been delayed by rising costs and budget constraints. Reuters quoted a government spokesman at the time as stating: “We will complete construction of the few remaining kilometres soon and we will do everything possible to make sure that the delay has no impact on production”
In addition to Fiat, BMW is another key customer for the logistics provider. Following a new components commission from BMW last year, DB Schenker Logistics is now increasing its Leipzig centre workforce by 700 and adding new warehouses. DB Schenker delivers CKD kits to BMW plants in China and South Africa. Since summer 2011, an estimated 8,000 different BMW automotive components have been received and packed at the 63,000 sq m Leipzig site. This extended capacity announcement is expected to see an increase from 50 to more than 100 containers being packed daily for shipment to plants in Shenyang, China, by rail, and Rosslyn, South Africa, by sea.
Megan Lampinen