As geopolitical tensions challenge and constrain established lithium-ion (Li-ion) battery supply chains, which are primarily consolidated in China, sodium-ion (Na-ion) is gaining attention in the automotive industry. Sodium is both 1,300-times more plentiful and 90% cheaper than lithium, making the batteries theoretically easier to scale around the world.
However, sodium has a larger molecular mass than lithium, making movement of ions between the cathode and anode during charge/discharge cycles slower. Furthermore, the voltage of a sodium chemistry cell is generally lower than lithium. These factors combine to halve Na-ion’s energy density relative to Li-ion, making it impractical for electric vehicle (EV) applications where range is a core customer purchase consideration.
For now, the race to create a commercial-scale Na-ion battery that can compete with Li-ion is still on. However, the finishing line might be closer than ever before.
‘Blank slate’ thinking
Mircea Dincă, Alexander Stewart 1886 Professor of Chemistry at Princeton University and leader of the Dincă Lab research group, has been exploring battery technology since 2015. Dincă Lab consists of around 20 staff, including PhD students and post-doctoral associates. Its focus on energy storage started with supercapacitors, devising new classes of materials previously unused in such applications. “We were outsiders to the community, but that was our advantage: we didn’t have decades of baggage to constrain us,” Dincă tells Automotive World.
It was this ‘blank slate’ that attracted Lamborghini to Dincă Lab, and the two began a relationship in 2017, while the latter was still part of the Massachusetts Institute of Technology’s (MIT) chemistry department. This subsequently transferred with the research group’s move to Princeton. Lamborghini was interested in new battery solutions for EVs and offered a broad remit for Dincă to explore options that would hit key metrics like power, energy density, and stability.
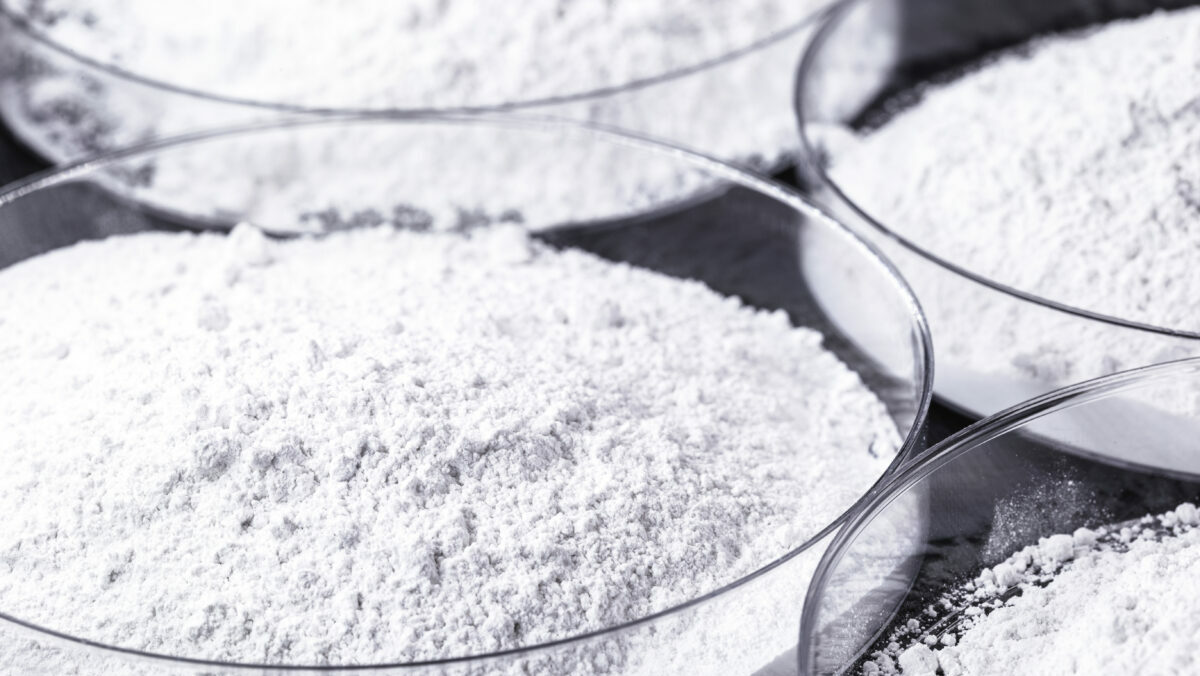
Other companies have investigated how to retain Na-ion’s low cost while boosting its performance. For example, California-based start-up Unigrid claims replacing carbon with tin in the anode can triple capacity and shrink its size by 1,500%. On the other side, Dincă Lab researched how new cathodes could improve Na-ion performance. “Finding solutions with multi-electron redox behaviour that enables multiple sodium ions per unit of cathode material was really difficult,” says Dincă. Nonetheless, in February 2025, this is exactly what his team demonstrated.
Solving performance issues
The solution’s foundation came in 2024 with the development of a new layered organic solid called bis-tetraaminobenzoquinone (TAQ). Dincă credits the achievement to the “educated guesses” of his staff and the “wide research latitude” facilitated by Lamborghini’s funding. The researchers published their findings in ACS Central Science, originally citing its potential in Li-ion applications. The TAQ molecule is both insoluble and highly conductive, qualities that make it well suited for use in cathodes, and this eventually shifted focus over to its prospects for solving Na-ion’s perennial performance issues.
Over the next year, Dincă Lab researchers—Tianyang Chen, et al—used carbon nanotubes to bind TAQ crystallites with carbon black particles. This yielded an interconnected and homogenous cathode that enables up to 100% utilisation of the active material. Importantly, the material has high cycling stability and is durable to air, moisture, and heat.
The research group’s 2025 paper on its findings, published in Journal of the American Chemical Society, claimed an electrode-level energy density of 606 watt-hours per kilogram at 90% weight of active material. A Na-ion cell had a cathode energy density of 472 Wh/kg when charged/discharged in 90 seconds. Theoretically, this could give it almost a 60% performance advantage over Li-ion cells using nickel-manganese-cobalt (NMC) cathodes, which generally achieve up to 300 Wh/kg. However, it should be noted that this comparison is currently based on lab scale versus manufactured products.
A true breakthrough?
Dincă believes TAQ cathodes in Na-ion batteries could enable the automotive industry to “hit all its battery performance targets at once.” The improved rate performance increases overall gravimetric and volumetric density, meaning batteries can be smaller and store the same amount of energy as current generation cells or be scaled up to store more. “How much space a battery takes up in a car is an important consideration. On top of that, automakers improve other aspects that customers will care about, like safety and cost.”
Talking about a battery’s cost or performance doesn’t mean anything if they aren’t in balance with each other
Exact pricing will be difficult to determine until Daqus Energy, a start-up spun out from MIT, of which Dincă is also a co-founder, has scaled TAQ production sufficiently for industrial manufacturing. However, the potential benefits for OEMs like Lamborghini are clear, and the company can afford to wait—it has pushed back the release of its first EV to 2029, expecting the market to mature further during the interim. A slight delay could save money and produce a better and wider variety of battery options in the long term.
“In principle, TAQ can replace cathodes in some of the higher-end but geopolitically problematic Li-ion battery chemistries like NMC,” states Dincă. “TAQ comes from commodity chemicals derived from petroleum, and access to those downstream products is very secure compared to metals. Wouldn’t it be better to make smart materials from petroleum instead of burning it?” In addition to allowing automakers to build more secure supply chains, synthesising TAQ is also less carbon intensive (involving heating up to 120 degrees Celsius) than NMC (up to 800 degrees Celsius).
By then replacing lithium with sodium—which is basically sea water—Dincă says that automotive can rid itself of all the “problematic minerals” that continue to plague battery production. “Talking about a battery’s cost or performance doesn’t mean anything if they aren’t in balance with each other. TAQ reconciles both in an environmentally friendly solution that complements broader electrification efforts.” This, he concludes, could be the true breakthrough of TAQ-based batteries.