It may have made a name for itself as a proponent of aluminium, but Ford is currently only using aluminium intensively for the body of the F-150 pick-up; with annual F-Series sales of 700-800,000 units, that represents around 12.5% of the 6.4 million ‘Blue Oval’ and Lincoln vehicle sales Ford reported in 2014.
A full-line vehicle manufacturer, Ford’s portfolio extends from the Ka city car right up to Class 7 commercial vehicles, as well the Cargo heavy truck. It would be impossible for an OEM of this size to introduce a group-wide material-specific lightweighting strategy. Instead, Ford focuses on design optimisation and the use of application-specific materials.
Ford’s efforts to reduce vehicle weight – which it calls ‘mass decompounding’ – have been well publicised: the GT launched in 2005 was the first all-aluminium Ford; in 2014, the OEM unveiled the Multi-Material Lightweight Vehicle concept developed with Magna and the US Department of Energy (DOE) and the aluminium-bodied F-150; and in 2015, the OEM unveiled the carbon fibre-bodied GT supercar.
“Fuel economy and CO2 regulations go hand in hand,” explains Matt Zaluzec, Ford’s Technical Leader, Global Materials and Manufacturing Research. “If we lightweight our vehicles and continue to push our powertrain strategy, the consumer will get CO2 reduction and fuel economy improvements.”
The right material for the right product
Zaluzec sums up Ford’s three-pronged approach to reducing vehicle weight as: “design it right, apply the right material on the right product at the right time, and put that together with the right powertrain. We look at the entire vehicle as a system.”
Reducing weight can be expensive, and balancing lightweighting with cost is something OEMs live with every day: what is the right material for the product, and what are the ways the OEM can offset cost? On the Ford GT, Zaluzec says, “We’re going to be using an extraordinary amount of carbon fibre. That’s good for the GT but not for an F-150.”
The impact of large commodity purchasing for expensive materials can be reduced by developing partnerships with major materials specialists. Smart production line management can also help: Ford, for example, collects all stamping waste metal, sorts the scrap into appropriate bins, and sells the aluminium cut-offs back to the aluminium supplier “at a premium.”
The business case for a new material hinges on the benefits. These can be classed as primary, secondary and tertiary benefits, explains Zaluzec; primary might be weight, for example, secondary could be safety and tertiary could be performance.
Any switch from steel to aluminium, or from aluminium to magnesium or to carbon fibre, comes with cost penalties. One way to offset costs is to consolidate parts. “By consolidating parts and using hydroforming instead of multiple stampings, there may be a material cost increase, but consolidating parts reduces capital expenditure and tooling costs.” It also addresses the cost, weight and process time of welding or bonding.
“Switching to a new product or material often requires an OEM putting new joining techniques into its plants. For example, combining steel and aluminium requires a combination of mechanical joining and adhesives. And so it comes back to the business case. Have we done the design optimisation first in steel? If we have, we’re going to move forward. There are numerous steel solutions out there for lightweighting. There are some advanced high-strength steels that are just wonderful, and we have those as part of our product plan – although I can’t tell you the vehicles.”
Any major material switch benefits not only the programme in question, but also cascades into other vehicle programmes within the group. In choosing to produce an aluminium-intensive body for the F-150, Ford “jumped in at the deep-end,” says Zaluzec. “We haven’t done a low volume niche vehicle – we’ve done one of the highest volume production vehicles in the world.” He adds that the switch to aluminium was not only to save overall weight – it was to enable improved towing, hauling, braking and acceleration without increasing overall weight.
The multi-material challenge: price, process, supply and demand
Carbon fibre may be lighter than an equivalent part in steel, but it is also more expensive. However, some of that cost can be absorbed through part consolidation, combining numerous parts and employing a composite processing technology rather than multiple stampings.
The benefits of using carbon fibre are offset by how much it costs per part to produce, and how quickly it can be produced, since the cycle time per part is slow compared to metal stamping. A third factor, adds Zaluzec, is supply and demand. “We need the price of carbon fibre to come down from aerospace grade costs to what we call industrial grade. US$5 to US$7 per pound (US$11-US$14/kg) starts looking attractive because we could find additional applications. But let’s put it into perspective: for a niche and specialty vehicles, carbon fibre is great. But the reason we did aluminium on the F-150 is because we sell hundreds of thousands of units annually. 750-800,000 units is not unheard of. There is not enough carbon fibre supply in the world to do the F-150, but there is enough aluminium.”
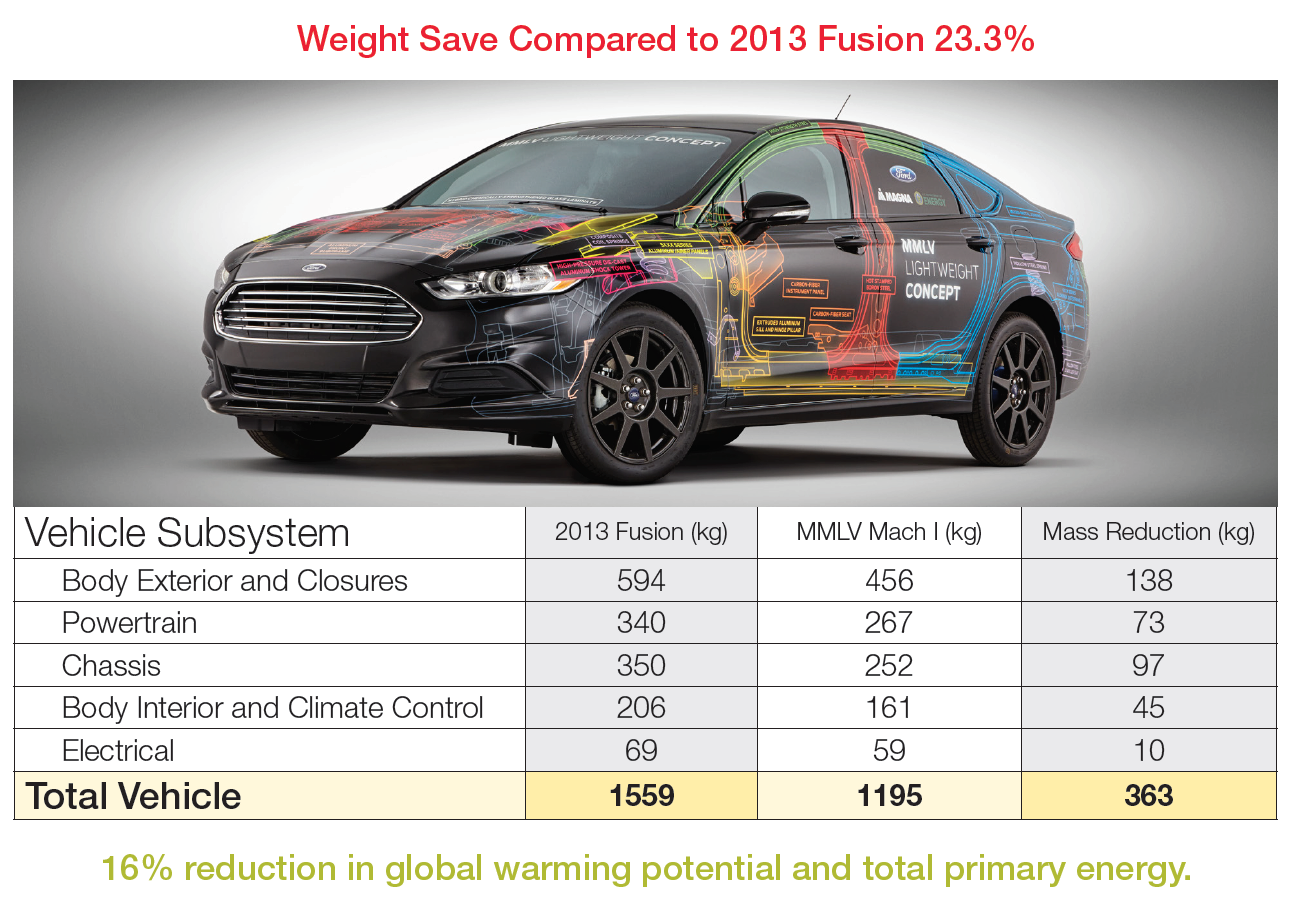
Nonetheless, Zaluzec confirms that he and his team are working on carbon fibre. “It’s got our attention and we have a number of researchers working on material, process and cost, and we have a good partnership with (carbon fibre supplier) DowAksa. Where I am today on carbon fibre and its different processes is where I was maybe 15 years ago on aluminium. In high volume applications, you’ll only see carbon fibre slowly creep in, but for low volume applications, you’ll see it more prominently used.”
Having addressed steel, aluminium and carbon fibre, the conversation turns to magnesium. “One of the challenges for magnesium is that, unlike aluminium and steel, magnesium comes primarily out of China. We need a guaranteed, continuous supply of it, and it’s coming from the other side of the world. There’s a supply and demand curve, and there’s a cost.” Magnesium offers some interesting opportunities, says Zaluzec, particularly high pressure die cast magnesium parts where part consolidation could offset cost. Research is being conducted into magnesium sheet metal applications, but corrosion remains a challenge, hence its use primarily for instrument panel carriers, steering wheels and some interior components.
Lightweighting is about more than just body weight
Whilst major steps are taken across the industry to reduce vehicle body weight, there are three areas of the vehicle in particular that present an ongoing challenge in terms of weight saving, namely glazing, seats and wiring.
Two technologies are being explored as a replacement for conventional, soda-lime glass: chemically toughened glass and polycarbonates. Ford has tested both, says Zaluzec, and ahead of putting chemically-toughened glass into series production, it is using it on the Ford GT supercar, thanks to a partnership with Corning and glass suppliers. Depending on the application on the GT, he explains, the first ever automotive industry application of Corning Gorilla Glass varies from a 35-37% weight saving through to as much as a 60% weight saving. And on the aforementioned MMLV concept, Ford reduced the weight of a baseline 2013 Ford Fusion to that of a Fiesta. “We took 23.3% weight out and included an entire complement of chemically toughened glass for the windscreen and the drop glass.” Like carbon fibre, says Zaluzec, the cost of the chemically toughened glass must come down to make it viable. Should it do so, it will migrate to higher intermediate or higher production vehicles.
Seats, says Zaluzec, present a considerable challenge: “Seats are so optimised right now in steel and it’s such an inexpensive material that it’s very hard to find a replacement. Aluminium technology is being explored for the seat itself and the structural element of the seat back. On the MMLV, we developed carbon fibre seats, and we are exploring opportunities to make injection moulded components for seats, some with glass fibre and with carbon fibre. The move from thermosets to thermal plastics for some future seat components is promising.”
Wiring harnesses – the groups of electrical cables running throughout the vehicle – can often weigh the equivalent of a large adult. “We’re always looking for solutions in wiring harnesses,” says Zaluzec. “The real issue is the reliability of the interconnects.” Ford has looked at alternatives, including aluminium, thinner copper coated wires and fibre optics, “but they’re not ready for prime time.”
Coming soon: more aluminium on more cars
In terms of the likely material mix for future automotive applications, Zaluzec expects an increase in the use of aluminium across the industry. “You’re going to see aluminium on more products, especially doors and hoods, from Ford and from our competitors.” In addition, OEMs will deploy more multi-material solutions. “It’s about creativity – are there places in a steel vehicle where I can introduce mixed materials? Or an aluminium vehicle with steel or carbon fibre reinforcements?”
As for carbon fibre, Zaluzec appreciates the benefits, but remains cautious – not so much of the cost but of the availability of the volumes required for mass-market automotive applications. “It’s going to take many years to grow the carbon fibre infrastructure to the point where there will be enough available at a certain price point to significantly impact overall vehicle weight. You’re going to see steel and aluminium really delivering much of the weight reduction.”
Given the lengths to which the OEMs and suppliers go to reduce vehicle weight, how do consumers respond to vehicle lightweighting? Do they even care? “Customers look at the price of the vehicle and the fuel economy, and then at the creature comforts. They generally get the benefit from lightweighting without even knowing it. If we’ve done our job right on a Fusion, a Focus, or an F-150, and the customer buys it, they’re buying it because it’s a durable, great looking functional vehicle, not because it’s lightweight.”
This article is part of an exclusive Automotive World report on lightweighting. Follow this link to download a copy of ‘Special report: Vehicle lightweighting‘