For the manufacturing world, electric vehicle (EV) batteries pose a variety of unique design considerations. Temperature regulation, for instance, is crucial in ensuring battery longevity and safety. A 2019 study by the American Automobile Association revealed that operating temperatures outside the optimal range of 20-40 degrees Celsius can reduce a battery’s range by 10-12%—and even as much as 41% if HVAC is used to regulate heat. Poor temperature regulation can also lead to thermal runaway, with fires that burn up to 1,000 degrees Celsius.
Nicholas Huff, Team Leader of New Technology Group at Sunstar Engineering Americas, believes that effective thermal management “requires an integrated solution from all the players involved.”. This includes all players involved in the battery cell chemistry: the pack manufacturers, electronics companies, OEMs, and adhesives companies. Focusing on the latter, Sunstar Engineering aims to facilitate the next generation of batteries through new innovations in thermally conductive materials.
All in the chemistry
One of the biggest challenges in supporting the thermal regulation of batteries is finding the most suitable compound for the adhesive mix. “There are as many chemistries as there are applications,” says Huff. Most adhesives have poor thermal conductivity on their own, but there are numerous additives that can be used to enhance their efficacy.
Polyurethanes, for example, have strong thermal properties and can double as a flexible underfill to connect components. Metal particles such as aluminium, silver and copper are among the best thermal conductors—however, these are a risky solution for batteries as they also conduct electricity. This could lead to a battery being shorted or the formation of an electric arc—a discharge of electricity between gaps in a circuit.
Ceramics, Howe highlights, do not have this issue. Boron nitride is a ceramic nitride that can conduct heat well without risk of discharge, but it is expensive. Ceramic oxides like alumina are cost-effective but less thermally conducive. However, depending on the heat generated by a battery pack, and the manufacturer’s budget for the adhesive, ceramics can still prove an effective solution.
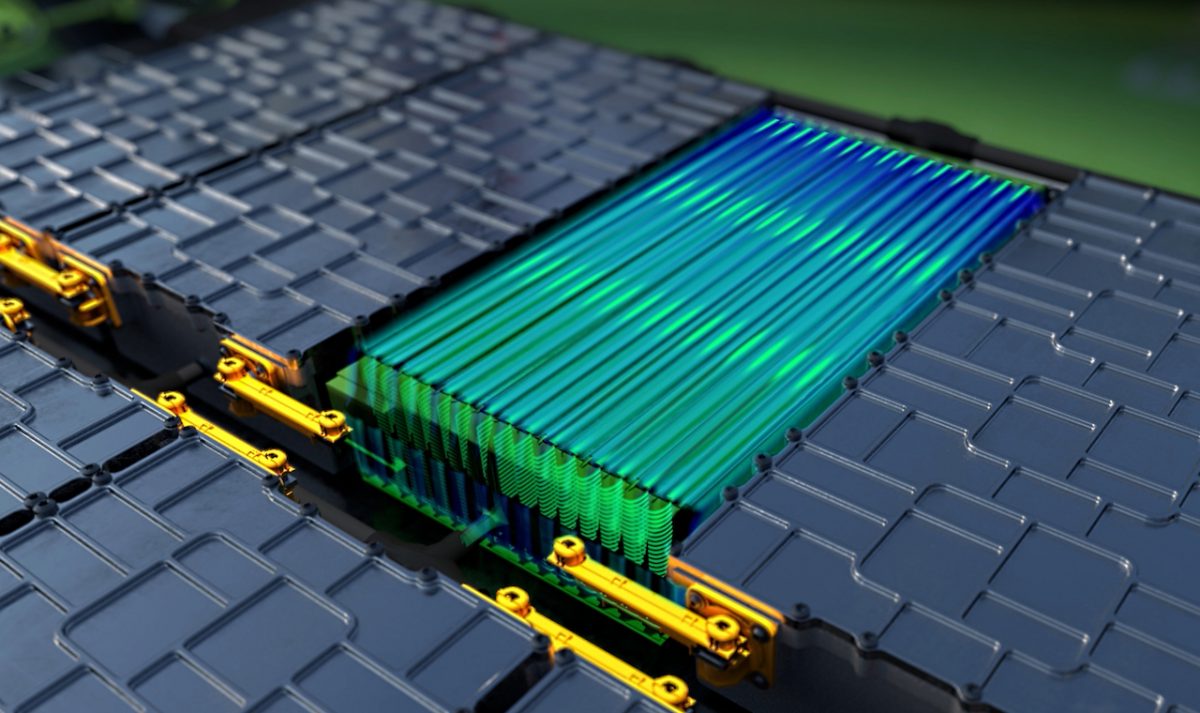
Huff believes that some of the most promising research has explored materials enhanced with silicon and carbon nanoparticles. “In terms of the more experimental applications in battery packs, these materials are of great interest.” Indeed, carbon nanotubes can increase the thermal conductivity of a synthetic oil substrate (used in liquid battery cooling) by 156%, according to a 2022 study featured in the journal Biomass Conversion and Refinery.
Ultimately, Huff remarks, there is no concrete answer as to which chemistry is most optimal for use in battery adhesives. As battery technology continues to develop, new compounds will need to be developed to meet their changing specifications and thermal requirements. Going forward, he emphasises that thermal conductivity will only be part of the equation.
Facilitating second-life
The increasing demand for sustainability in batteries means that it is also important to ensure that the adhesives used facilitate second-life use and recycling. Being able to extract and repurpose materials such as lithium necessitates the use of a ‘debondable adhesive’, which, when exposed to certain conditions, will lose its bonding properties and allow a battery pack to be opened.
“The trick is making sure that those conditions don’t come up during the battery’s normal usage,” Huff states. Sunstar Engineering is currently working on a project with an unspecified major OEM to deliver a suitable debondable adhesive. Sunstar Engineering is also investigating options with an unnamed university to make a bio-based version of this foaming material that sources its polymers from nature. “We hope to implement this technology for next generation battery designs,” he says.
It’s a team effort
Adhesives cannot effectively cool a battery in isolation. Thermal management systems for EV batteries have been the subject of intensive research and testing in recent years. Huff believes some of the most promising developments have been in liquid cooling. Direct liquid cooling (where cold water is continuously fed through a battery-mounted plate) has been shown to offer more effective thermal transfer than indirect liquid cooling or air cooling. More advanced sensors are also being developed that can isolate potentially faulty cells and shut them down before thermal runaway occurs.
Adhesives companies can act as facilitators for such developments. “As battery pack designs change to enable better cooling strategies, adhesives must also change to incorporate better performance and handle the thermal and mechanical stresses inherent to new applications,” Huff explains.
The EVs of today won’t be like the EVs of yesterday. We’re going to need an all-hands-on-deck approach
In direct liquid cooling, for example, the cooling plate cannot make direct physical contact with the battery itself, as it will quickly lead to overheating. Instead, a compatible intermediary adhesive must fill the gap between the two parts to ensure that temperatures remain stable. The higher the thermal conductivity of the paste, the more efficient it will be in heat dissipation. Furthermore, the volume of material depends on the expected thermal load from the battery, the heat capacity of the plate, and the conductivity of the paste itself.
There is no one-size-fits-all solution for every use case. As EVs continue to evolve, Huff concludes that it will be essential for all industry players to collaborate on integrated thermal management systems that meet the changing requirements of batteries. “The EVs of today won’t be like the EVs of yesterday. The successful transition to electrification will be a community-wide effort.“