The Inflation Reduction Act continues the recent trend of the federal government stressing its commitment to the domestic manufacturing of electric vehicles (EVs) and batteries. The bill provides US$30bn in production tax credits to bolster manufacturing of clean energy technologies in the US, including batteries and critical mineral processing. It also dedicates a US$10bn investment tax credit to build clean technology manufacturing facilities, such as EV factories, among other funding allocations. This complements the US Department of Energy’s announcement earlier this year that dedicated US$3.1bn from the Infrastructure Investment and Jobs Act to be used to support the build-out of a domestic critical mineral supply chain that will support battery and EV production.
These announcements are just the latest in a series of efforts by the Biden administration to encourage the development of domestic supply chains for critical materials used to make lithium-ion batteries, the dominant battery technology used to power today’s EVs. Domestically sourcing batteries and EVs brings major benefits, such as curtailed geopolitical risks, domestic job creation, and accelerated EV adoption.
Considering the current reliance on lithium-based batteries using materials sourced from abroad, is it even possible for domestically manufactured EVs to reach cost parity with conventional vehicles?
Despite all of this, prices for these battery materials have surged in recent months, and analysts expect them to rise further over the next few years. With the battery pack accounting for approximately 40% of the entire cost of an EV, automakers like Tesla, Rivian, and Cadillac have been pushed to raise the prices of their Evs, making EVs even more unaffordable than they already were for a majority of Americans. This inhibits the widespread adoption of EVs, the opposite of what’s necessary to make a meaningful impact on emissions.
Beyond funding for domestic manufacturing, the Inflation Reduction Act also includes tax credits for consumers who buy used and new EVs. However, EV buyers are only eligible to earn these credits on the purchase of American-made cars, and only if the majority of battery components come from North America, and contain a certain percentage of minerals from countries with free trade agreements with the US (which does not include China and Russia, nor any of the African countries where more than 70% of all cobalt is sourced). As it stands now, most finished EV batteries are produced in China, or rely on lithium and cobalt that’s processed there. Metals mined and processed in North America will undoubtedly be more costly, potentially making batteries even more expensive—not less.
This raises the question: considering the current reliance on lithium-based batteries using materials sourced from abroad, is it even possible for domestically manufactured EVs to reach cost parity with conventional vehicles? According to the US Department of Energy’s Vehicle Technologies Office, battery costs need to fall by more than 50% to US$60 per kWh for an EV’s total cost of ownership to reach US$0.26 a mile, compared to US$0.27 for a conventional vehicle with an internal combustion engine.
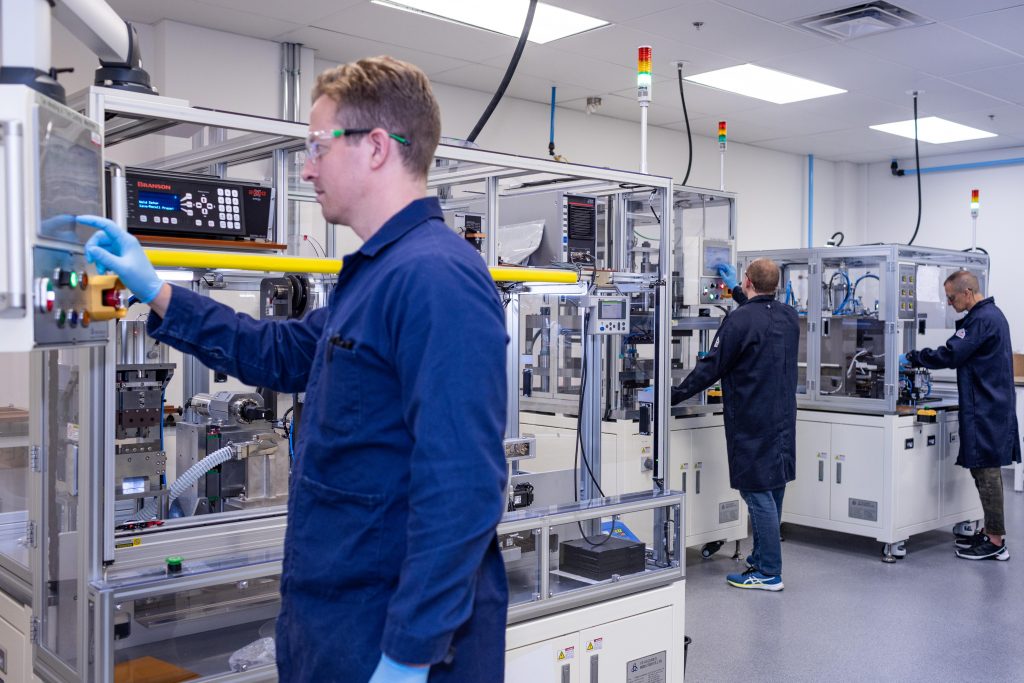
In order to make domestic, affordable EV and battery manufacturing a reality, automakers need to explore the use of lower-cost, readily available materials with more predictable supply chains. This will allow manufacturers to avoid price fluctuations due to geopolitical scenarios as well as reduce shipping costs to transport these materials to processing and manufacturing facilities. These materials also need to cost less than lithium while offering the same quality of performance. Ideally, they would also be safer and better for the environment.
These alternatives exist. Policymakers and automakers should keep a keen eye to the diverse materials being used to build clean technologies—specifically batteries—and focus funding towards building domestic supply and manufacturing for these game-changing battery materials. These lithium battery alternatives can be the key to building a cost competitive domestic supply chain for EVs and EV batteries. Because in the end, we want to make our EVs and batteries in America, and we want every American to be able to afford one.
The opinions expressed here are those of the author and do not necessarily reflect the positions of Automotive World Ltd.
Mukesh Chatter is Co-Founder and Chief Executive at Alsym Energy
The Automotive World Comment column is open to automotive industry decision makers and influencers. If you would like to contribute a Comment article, please contact editorial@automotiveworld.com