Corrosion-related component failures in modern industrial automation systems have become a costly problem in tyre and rubber plants worldwide. If industrial system corrosion sounds like a niche problem, it’s worth remembering that such issues cost an estimated US$2.5tr globally, according to the Association for Materials Protection and Performance.
Corrosion can wreak havoc on the complex and highly miniaturised electronics that are now found in most industrial automation products. For reasons that have only recently been uncovered, this corrosion process seems to be further exacerbated in tyre manufacturing settings, and the gaps in understanding have inhibited developing consistent and reliable approaches to mitigating the problem.
The good news is that, as we continue to clarify the industry-specific reasons for corrosion of industrial components in tyre manufacturing, these insights are informing better testing and modernisation efforts for tyre producers to better pinpoint the source of corrosion problems in their plants. These discoveries can then guide strategic upgrades to industrial components and processes to effectively combat corrosion and improve machine efficiency, uptime and reliability.
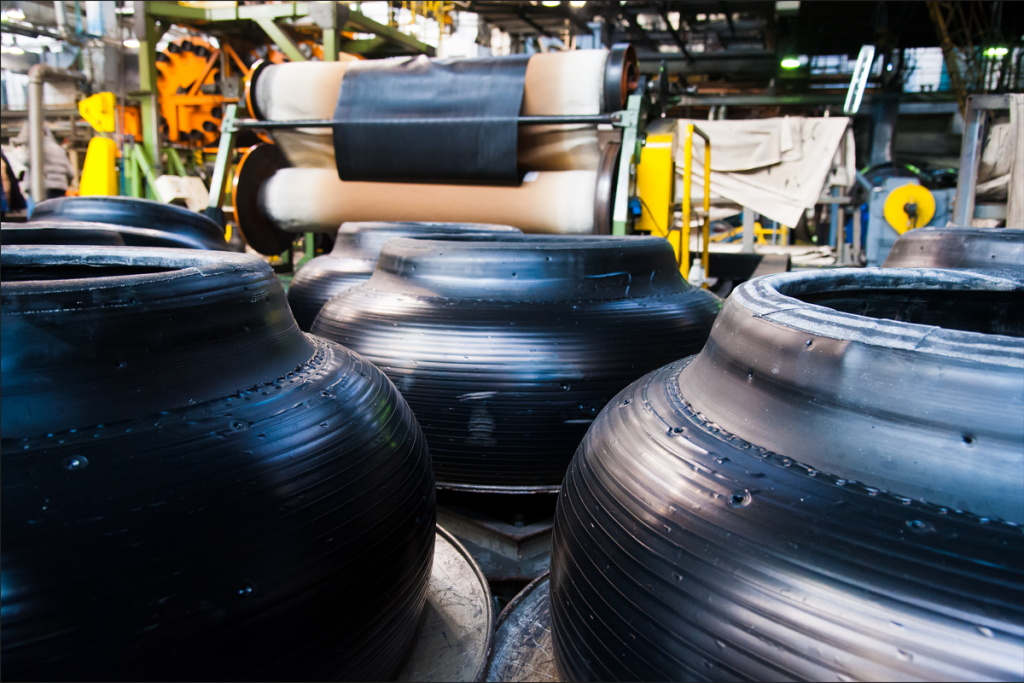
Hidden causes to a major production challenge
The miniaturisation of electronics in recent years has transformed manufacturing capabilities across many sectors, and the industrial control products used in tyre and rubber production facilities are no exception. Miniaturisation in these settings has allowed for more connected, data-driven and higher-performing operations with a minimal footprint on the plant floor.
Unfortunately, this evolution in industrial electronics has also created an unexpected challenge in the form of corrosion. Specifically, as the industrial control products used in tyre and rubber plants have become smaller and more densely packaged, they are more prone to corrosion-related failures.
At first glance, the cause of this is an industrial mystery. The corrosion problem has shown no bias, affecting a wide range of automation products and vendors. Corrosion has also been found in every part of the tyre production line and in plants around the world, causing unplanned downtime and impacting key production performance indicators like overall equipment effectiveness (OEE). Even though suppliers have created industrial control components designed to survive in corrosive environments, somehow the products have proven to be particularly inconsistent and unreliable when operating in tyre and rubber plants.
The mystery is finally being solved by close examination of these factory environments and some unique characteristics of the rubber production process that contribute to corrosion. It turns out that atmospheric reactive compounds generated in the tyre-making process are combining with temperature and humidity factors to cause rampant corrosion on the electronic components of industrial control products. These reactive compounds have always been present in tyre plants; however, they are having a greater impact in today’s miniaturised world of industrial control products that require more airflow across more tightly packed electronics and circuit boards. This creates a perfect storm for corrosion—a unique manufacturing challenge that requires a uniquely tailored and strategic approach to solve it.
Understanding corrosion causes drives better solutions
Armed with an enhanced understanding and the right industry partners to address the corrosion challenge in their industrial systems, tyre manufacturers can transform their control architectures with a two-pronged approach: one that combines corrosion-resistant product enhancements with sealed enclosures to better protect product control systems against the elements that are causing the corrosion.
A control architecture can deliver improved performance in tyre plants by adding design features like conformal coating to reduce the impact of corrosion-causing atmospheric contaminants. Conformal coating involves spraying a non-conducting insulator onto a device or component within a product. The insulator “conforms” to the assembly’s profile and helps protect it from corrosive gases, humidity and other environmental stresses.
If industrial system corrosion sounds like a niche problem, it’s worth remembering that such issues cost an estimated US$2.5tr globally
This conformal coating can be combined with several other design modifications to create an “extra tough” grade of product protection against corrosion, and many companies are already seeing the benefits of these enhancements. For example, a major tyre maker experiencing a corrosion-based failure every 16 to 18 months made the move to “extra tough” drives as part of a reliability programme. To date, the company has fielded more than 100 of the drives, many of which are still running smoothly after years of use.
On their own, even the toughest corrosion-resistant assembly upgrades aren’t enough to fully combat corrosion in the push to increase OEE and reduce downtime risks in tyre plants. Robust, sealed enclosures are the key to delivering an essential second layer of protection. A combination of top quality enclosures and optimised installation and maintenance of these enclosures in manufacturing systems can guard against the environmental conditions that would otherwise subject tyre manufacturing components to extreme corrosion.
For example, sealed grommets and fittings can be used to seal cables that enter or exit an enclosure. Steps like these can help prevent contaminants from entering and building up inside an enclosure. It’s also critical to follow manufacturers’ installation instructions for minimum mounting clearances. That’s because heat-generating devices that are mounted with an improper clearance will not only increase corrosion, but also lead to failures resulting from overheating.
Enhanced testing drives better corrosion solutions
Especially when implemented together, these corrosion-fighting strategies help protect control systems and reduce failure-related downtime. But knowing exactly where, when and how to deploy these enhancements across vast tyre production networks requires enhanced test protocols. Throughout it’s important to remember that, in the process of designing any new test protocol, the correct balance must be struck between producing the required results and being able to conduct tests within a reasonable time period.
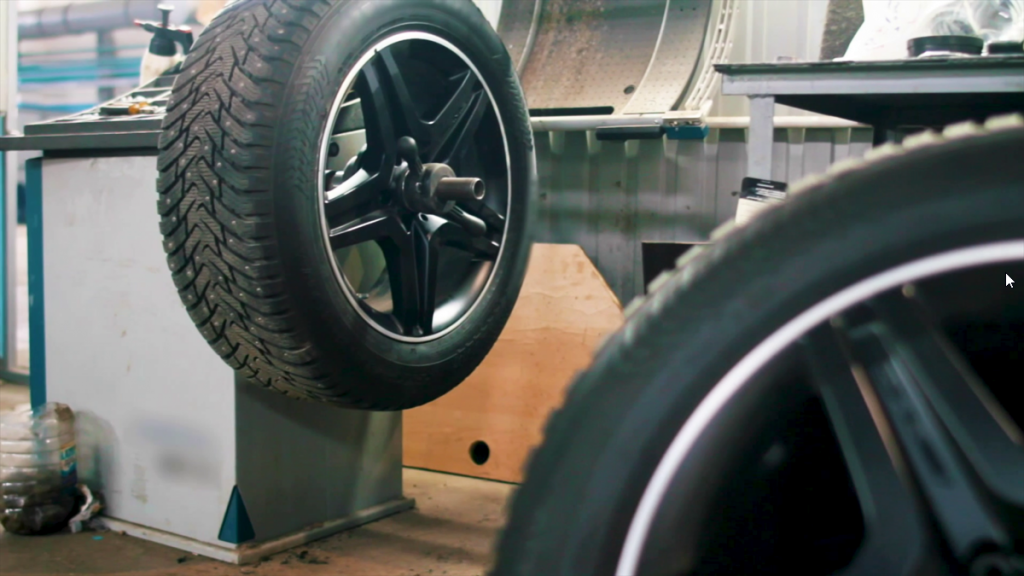
Testing should be tailored to the unique manufacturing environment and be designed to both evaluate the effectiveness of current products against corrosion and support the development of new mitigation strategies if needed. Consider the use case of mixed flowing gasses (MFG) testing in tyre manufacturing to identify the problematic compounds that contribute to corrosion in that specific production setting. After many iterations and by adjusting certain test parameters, it’s possible to accelerate different corrosion rates and affect corrosion composition on different metals.
These testing insights then helped drive the development of a new MFG exposure chamber that incorporates an extended temperature range significantly above and below ambient temperatures. The reaction area of the chamber was designed to not degrade with high contaminant concentration, while allowing for control of up to ten gas deliveries into the chamber. The reaction chamber was also significantly larger than the initial chamber used for testing.
In order to take on the significant corrosion problems disproportionately affecting factory environments compared to the rest of manufacturing, tyre producers must embrace the right testing and implementation resources to optimise both the materials and processes required for a more corrosion-resistant manufacturing setting. A better understanding of corrosion in tyre and rubber production environments is resulting in the development of new test protocols that go beyond industry-standard accelerated corrosion tests in order to be more representative of these tough production environments. This, in turn, is driving the development of more corrosion-resistant materials, components and installation protocols—all of which helps slash downtime and transform tyre production into a more efficient, durable and cost-effective operation.
About the author: Dan Paul is Global Business Leader, Tyre Industry, at Rockwell Automation